Press-center
Press-center
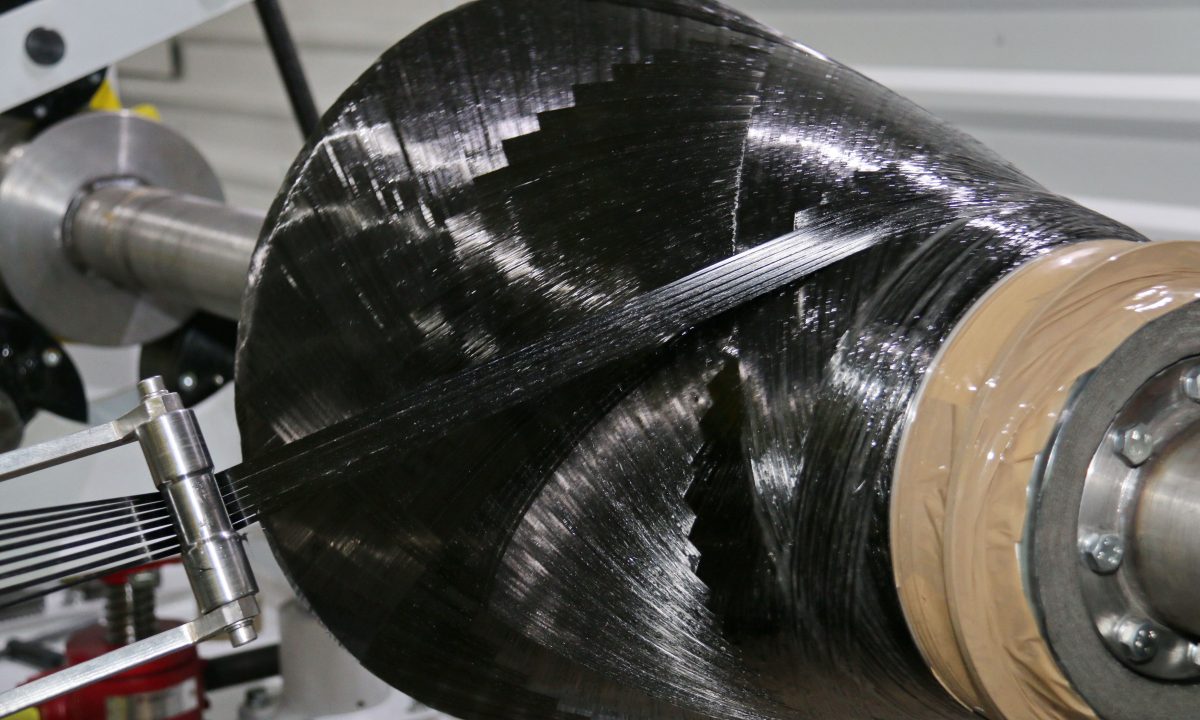
YUZHNOYE SDO DEVELOPS NEW SPACE ROCKETRY MANUFACTURING TECHNOLOGIES USING COMPOSITE MATERIALS
Creation of competitive space rocketry today requires new materials engineering and design solutions, adoption of new advanced technologies, and modern production base.
For this purpose, in 2015, at Yuzhnoye SDO, organization of pilot production was commenced – just at that time, in the frameworks of commercial contracts, Yuzhnoye SDO began purchasing and mastering new equipment. Now we may say about a new phase of this process: a whole division was created at the company, which will expand more, but already now, here, the new technologies of manufacturing space rocketry assemblies and parts of polymer composite materials (PCM) are being introduced which allow decreasing the mass of a structure and herewith improving its mechanical characteristics.
The division includes modern high technology equipment:
5-coordinate winding machine with working diameter up to 1 m and length up to 6 m, the Ukraine’s single high-precision 5 –axis processing center, impregnation machine for making semi-finished items (prepregs) of various reinforcing fillers, the first in Europe 3-D printer for making large-size PCM parts, painting-and-drying chamber and 40-atmospheres press-chamber, mobile coordinate measuring machines et al. This division ensures closed manufacturing cycle of modern space rocketry products made of polymer composite materials.
For the purpose of ensuring mass efficiency of the earlier developed reinforced-plastic spherical bottles with organic plastic shell, the works were performed to replace steel liner with plastic liner, and reinforcing organic fiber with high-strength carbon fiber. This technological solution is being already introduced in new developments.
The same applies to the dimensionally stable tubular elements that are used for assembling the spacecraft. Now, they are manufactured by method of spiral winding of high-strength carbon fiber. These components of satellite structure have already confirmed their operability in the conditions of space in wide temperature range. Today, these solutions are already being introduced in the design of future Sich-2M SC.
Besides, Yuzhnoye SDO masters the production of new advanced products – propellant tanks intended for storage of cryogenic propellant components in the temperature range from -196 to +100°С.
The pilot design of propellant tank that was manufactured at Yuzhnoye SDO is the all-wound plastic structure consisting of film liner, load-bearing shell based on carbon fiber and steel flanges. The tank was demonstrated at the international exhibition in Germany (April 2018).
The next efforts were directed at the development of designs of liner-free propellant tanks for the purpose of their weight improvement and ensuring leak-tightness of the entire structure. The liner-free tank was created in the form of all-wound plastic structure consisting of carbon flanges manufactured by method of outlay. The outlay technology was already used during manufacturing the Antares launch vehicle thermostating system parts made of carbon plastic and load-bearing shell based on carbon fiber. The functional tests were successfully conducted at loading with internal pressure up to 7.5 kgf/cm ². The tank was demonstrated at the international exhibition in China (November 2018).
The development of pilot production and the use of new materials and technologies allow our company increasing competitiveness of our products and remaining a strong player on the space services market.