Cyclone family
Cyclone family
Cyclone-4М
medium-lift
CLASS OF LAUNCH-VEHICLE
5 t
PL (Hcirc=200km, i=45,1˚)
39 m HEIGHT | 3.9 m DIAMETER |
260 t
MASS
Cyclone-4М
medium-lift
CLASS OF LAUNCH-VEHICLE
5 t
PL (Hcirc=200km, i=45,1˚)
39 m
HEIGHT
3.9 m
DIAMETER
260 t
MASS
DESCRIPTION
Cyclone-4M ILV is a two-stage monoblock medium-lift rocket. It is developed to place spacecraft into the low, medium and high near-Earth orbits, including sun-synchronous.
Existing technologies and procedures were used to the full in the development of the integrated launch vehicles and space launch systems, providing high reliability and production availability, minimal period of design and reasonable costs both during development and operation of the space launch system.
ILV development relies on existing or earlier developed details, units and parts. Such approach significantly reduces development costs and time.
ILV structure derives tanks and main components from Zenit and Antares rockets and has diameter of 3900 mm, applicable in serial production of ILV of Zenit and Antares families.
First stage design uses four Yuzhnoye-developed RD870 engines, running on liquid oxygen and kerosene as propellants. PA Yuzhmash has already mastered the production of the engine main components, which are being manufactured for other engines.
Second stage uses standard Cyclone-4 Stage 3, currently finalizing the ground development testing. It is equipped with RD861К engine, running on storable propellants NT+UDMH.
Upper stage is derived from Cyclone-4 rocket. Upper stage has passed the full cycle of ground development testing. Avionics components are developed on the basis of Cyclone-4 systems. They passed ground development testing and flight tests integrated with Dnepr rocket.
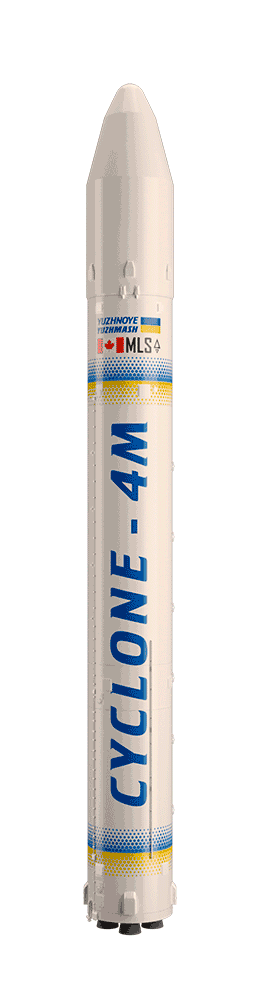
DESCRIPTION
Cyclone-4M ILV is a two-stage monoblock medium-lift rocket. It is developed to place spacecraft into the low, medium and high near-Earth orbits, including sun-synchronous.
Existing technologies and procedures were used to the full in the development of the integrated launch vehicles and space launch systems, providing high reliability and production availability, minimal period of design and reasonable costs both during development and operation of the space launch system.
ILV development relies on existing or earlier developed details, units and parts. Such approach significantly reduces development costs and time.
ILV structure derives tanks and main components from Zenit and Antares rockets and has diameter of 3900 mm, applicable in serial production of ILV of Zenit and Antares families.
First stage design uses four Yuzhnoye-developed RD870 engines, running on liquid oxygen and kerosene as propellants. PA Yuzhmash has already mastered the production of the engine main components, which are being manufactured for other engines.
Second stage uses standard Cyclone-4 Stage 3, currently finalizing the ground development testing. It is equipped with RD861К engine, running on storable propellants NT+UDMH.
Upper stage is derived from Cyclone-4 rocket. Upper stage has passed the full cycle of ground development testing. Avionics components are developed on the basis of Cyclone-4 systems. They passed ground development testing and flight tests integrated with Dnepr rocket.
FEATURES
Cyclone-4М | |
Number of stages | 2 |
Dimensions, mm | |
length | 39000 |
body diameter | 3900 |
fairing diameter | 4000 |
Launching mass (without PL), ton | 260 |
Propellants | |
Stage I | LOX + kerosene |
Stage II | NT + NDMH |
ILV engines: | |
Stage I | 4хRD870 |
Stage II | RD861К |
Engine thrust, tonf | |
Stage I | 318,8 |
Stage II | 7,916 |
Maximum weight of the injected payload, ton | |
Circular (Нcir=200 km, і=45,1°) | 5 |
Sun-synchronous (Нsso=700 km, і=98,16°) | 3,3 |
FEATURES
Cyclone-4М | |
Number of stages | 2 |
Dimensions, mm | |
length | 39000 |
body diameter | 3900 |
fairing diameter | 4000 |
Launching mass (without PL), ton | 260 |
Propellants | |
Stage I | LOX + kerosene |
Stage II | NT + NDMH |
ILV engines: | |
Stage I | 4хRD870 |
Stage II | RD861К |
Engine thrust, tonf | |
Stage I | 318,8 |
Stage II | 7,916 |
Maximum weight of the injected payload, ton | |
Circular (Нcir=200 km, і=45,1°) | 5 |
Sun-synchronous (Нsso=700 km, і=98,16°) | 3,3 |
Payload fairing
The payload fairing protects the payload from thermal and aerodynamic loads during launch vehicle ground
operations, liftoff, and flight. The payload fairing structure comprises two full-metal halves attached to each
other with retaining devices that are getting unfastened right before payload fairing jettison.
Spacecraft and payload adapters
The spacecraft adapter is used for the mechanical attachment of the spacecraft to the launch vehicle
and for spacecraft separation. The payload adapter mated to the payload fairing and the spacecraft
adapter forms a dust- and moisture-proof volume that maintains the required environment for the spacecraft.
RD861K
The RD861K is a single-chamber main engine designed for five burns, with a turbopump propellant-feed system.
The RD861K is not a staged combustion engine but uses the injection of the preburner exhaust gas into the
supersonic section of the nozzle. Thrust vector control is done by swiveling the engine in its gimbal suspension
in two mutually perpendicular planes.
Stage 1 Core Structure
The Stage 1 Core Structure is made of an aluminum alloy with reinforcement across the entire structure.
The stage burns environmentally friendly propellants that are kerosene and liquid oxygen.
The Stage 1 structure is based on the main components designed for the Antares rockets.