Interplanetary Missions Engineering
Interplanetary Missions Engineering
Interplanetary Missions Engineering
Moon Exploration
Lunar Spacecraft
6U CUBESAT SATELLITE
6U CubeSat satellite
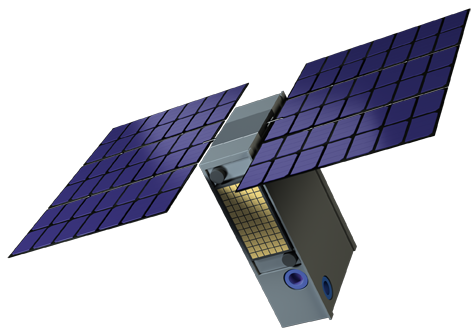
DESCRIPTION
SATELLITE BASIC SPECIFICATIONS
Satellite mass, kg | no more 14 |
Power supply system capacity, W | |
average | 60-65 |
peak | up to 130 |
Accuracy of the angular attitude, º | 0.5 |
Accuracy of the angular stabilization, º/s | 0.005 |
Active lifetime, years | 1 |
12U CUBESAT SATELLITE
12U CubeSat satellite

DESCRIPTION
SATELLITE BASIC SPECIFICATIONS
Satellite mass, kg: | no more 20 |
Power supply system capacity, W | |
average | 180 – 200 |
peak | up to 230 |
Main propulsion system: | |
working medium | Iodine |
thrust, N | 2× 1.24·10-3 |
total impulse, N·s | 2× 3.7·104 |
Accuracy of angular attitude, º | 0.5 |
Accuracy of angular stabilization, º/s | 0.005 |
Active lifetime, years | 3 |
Lunar lander family
LIGHTWEIGHT LUNAR LANDER
Light-
weight lunar
lander
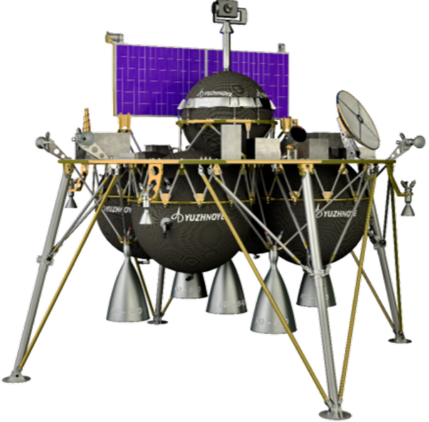
DESCRIPTION
The lightweight lander will deliver research equipment or a lightweight lunar rover to the surface of the Moon and carry out the lunar surface research at a landing site.
The lander can deliver a 50-kg payload to the lunar surface and transmit information received by the research equipment on Earth.
The lunar lander is based on the RD840 main engine.
The lander will be operational on the lunar surface for no less than 14 days.
FLYING LUNAR LANDER
Flying
lunar
lander
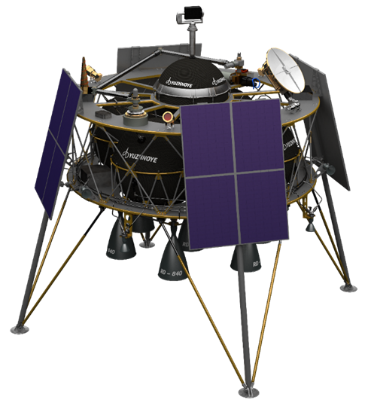
DESCRIPTION
The flying lunar lander designed by Yuzhnoye State Design Office will be used for commercial operation and research of the lunar surface at several sites in a single expedition.
The lander can deliver a 50-kg payload (scientific instrumentation) to the lunar surface, carry out research at the landing site, then take off and fly to a new site on the lunar surface.
In total, the lander can support research at up to three sites on the lunar surface, spaced about 20 km apart. The lander can visit two different sites (with a total of three soft landings).
The lander can deliver scientific instrumentation weighing up to 150 kg to the lunar surface without further flights to new areas.
The lunar lander is based on the RD840 main engine.
The lander will be operational on the lunar surface for 14 days from the landing.
MEDIUM-WEIGHT LUNAR LANDER
Medium-weight
lunar lander
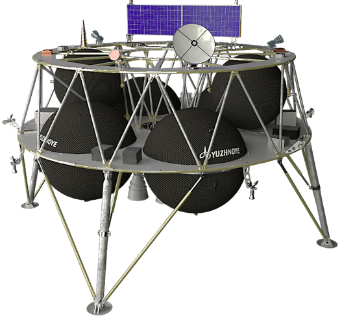
DESCRIPTION
A medium-weight lunar lander will deliver to the lunar surface the experimental equipment, mobile laboratories, cargo for the Lunar Base, etc.
The medium-weight lunar lender can be expendable or reusable.
The expendable version can deliver payloads from geotransfer or translunar orbit to the lunar surface.
The reusable version can deliver payloads from a circumlunar orbital station to the Lunar Base on the surface and return the lander to the orbital station.
The lander includes the RD860M main engine developed by Yuzhnoye State Design Office.
The lander will be operational on the lunar surface for no less than 14 days.
HEAVY LUNAR LANDER
Heavy
lunar lander
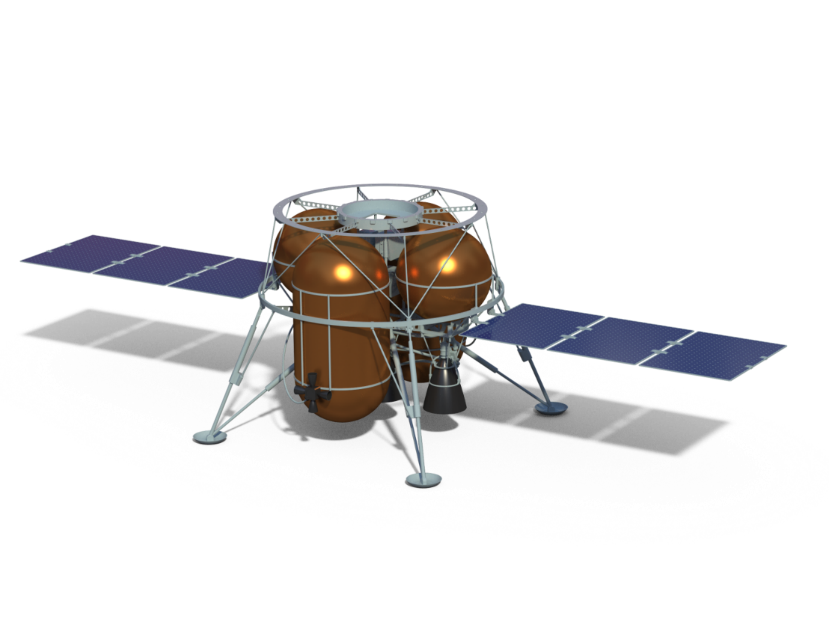
DESCRIPTION
The heavy lunar lander will deliver the delivery transport and the universal module to the lunar surface.
The universal design of the heavy lunar lander will accommodate delivery of both the Lunar Base modules and other payloads weighing up to 10 tons and manned vehicles.
Line of research rovers
LINE OF RESEARCH ROVERS
Line of
research rovers
DESCRIPTION
Features of the line of research rovers:
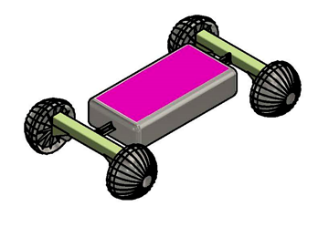
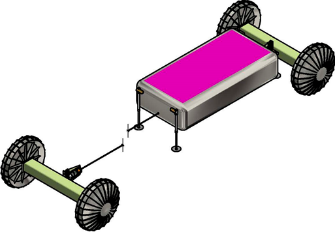
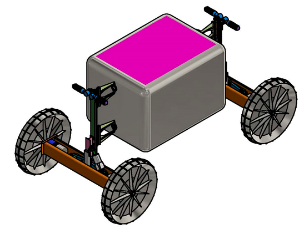
Moon Colonization
Space Transport System
Super-heavy LVs
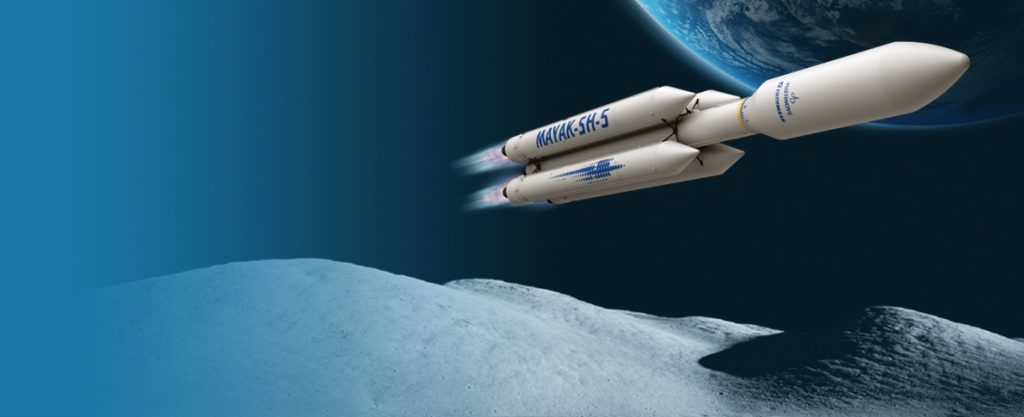
launch vehicles
Mayak-SH5,
Mayak-SH7
DESCRIPTION
The Mayak-SH5 and Mayak-SH7 space launch systems are designed for lifting the large-size spacecraft and components of orbital infrastructure, including those of lunar transportation systems, to near-earth orbits.
Burning liquid oxygen and kerosene, the Mayak-SH5 and Mayak-SH7 launch vehicles have serial staging and the design of the Mayak-S3.9 medium-lift launch vehicle enhanced with, respectively, 4 and 6 boosters whose structure is derived from the first stage of Mayak-S3.9. If necessary, these launch vehicles can have a booster for ascending directly to the trajectories towards the Moon and Mars, or a space tug for getting to lunar and near-Mars orbits.
The Mayak-SH5 and Mayak-SH7 launch vehicles operate the RD815 propulsion system in the first stage and the RD872 propulsion system in the second stage, both propulsion systems being developed by Yuzhnoye.
The launch vehicles have a payload fairing 6.2 m in diameter and 25 m long, made of a carbon fiber reinforced polymers. If required, a larger payload fairing can be provided.
SATELLITE BASIC SPECIFICATIONS
Launch vehicle | Mayak-SH-5 | Mayak-SH-7 |
Liftoff mass not including the payload, t | 2 246 | 3 101 |
Diameter of stages (fairing), m | 3.9 (6.2) | 3.9 (6.2) |
Propellants | LOX+kerosene | LOX+kerosene |
Launch vehicle height, m | 80 | 80 |
Stage 1 and booster propulsion | 15×RD815 | 21×RD815 |
Stage 2 propulsion | RD872 | RD872 |
Liftoff thrust, tf | 3 769.8 | 5 277.72 |
Maximum payload to orbit, t | ||
– circular orbit (Нcirc=200 km, i=51.6°) | 94 | 133 |
– lunar trajectory | 30* | 40* |
* using a specially designed booster
LUNAR BOOST STAGE (LBS)
Lunar boost stage (LBS)
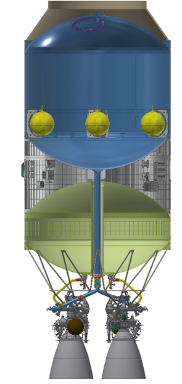
DESCRIPTION
The boost stage accelerates the transportation system up to the speed required to reach the Moon.
The boost stage is based on two RD809K engines.
SPECIFICATIONS
LBS liftoff weight (with payload), tons |
92.6 |
Stage propellants | LOX + kerosene |
Main engine nominal vacuum thrust, tnf |
2×10 |
Engine nominal vacuum specific impulse, s |
352 |
Stage length × diameter, m | 15.5×3.9 |
Payload mass delivered to translunar trajectory, tons |
30.5 |
LUNAR BOOST TUG
Lunar boost tug
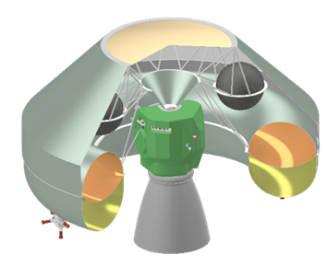
DESCRIPTION
The lunar boost tug (LBT) corrects the trajectory and supports entry into lunar orbit.
The tug is based on the RD861K engine.
SPECIFICATIONS
LBT liftoff weight (with payload), tons |
30.5 |
Stage propellants | NTO+UDMH |
Main engine nominal vacuum thrust, tnf |
7.9 |
Engine nominal vacuum specific impulse, s |
330 |
Stage length × diameter, m | 2.5×3.9 |
Payload mass delivered to lunar orbit, tons |
21.3 |
LANDING PLATFORM
Landing
platform
DESCRIPTION
The landing platform will deliver the Lunar Base components (unmanned mission configuration) and the lunar cockpit (manned mission configuration) from a lunar circular orbit to the lunar surface, ensuring their soft landing.
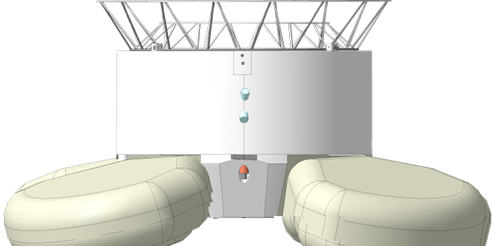
UNMANNED MISSIONS CONFIGURATION
SPECIFICATIONS
Propulsion system, tons | 0.3 |
Control, measurement, power supply, navigation, communication, temperature control, landing systems, tons |
0.4 |
Structure, tons | 0.7 |
Propellant, tons | 8.6 |
Total, tons | 10 |
Payload mass delivered to lunar orbit, tons |
21.3 |
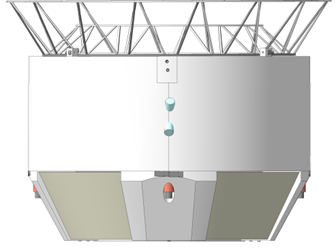
UNMANNED MISSIONS CONFIGURATION
SPECIFICATIONS
Propulsion system, tons | 0.2 |
Control, measurement, power supply, navigation, communication, temperature control, landing systems, tons |
0.5 |
Structure, tons | 0.2 |
Propellant, tons | 5 |
Total, tons | 5.9 |
SUPPLY SPACECRAFT
Supply spacecraft
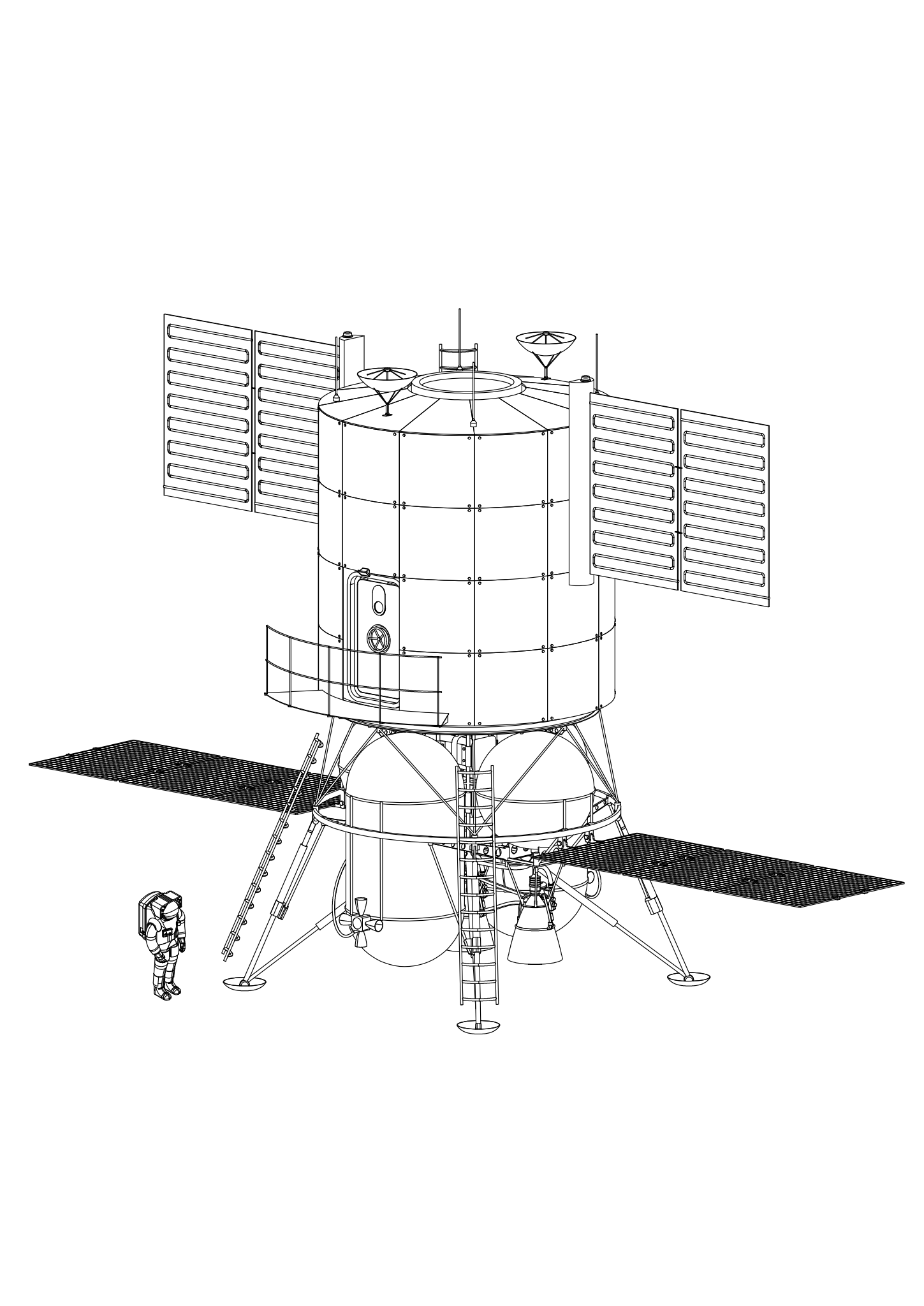
DESCRIPTION
The delivery transport is designed for periodic delivery to the Lunar Base of consumable supplies, equipment, tools, and spare parts, that is, everything that will be required but cannot be obtained from local resources.
Also, the transport can supply cargo from lunar orbit for landing expeditions in the desired areas (not related to the activities of the Lunar Base personnel).
The transport will be derived from the universal module using its body, antiradiation and antimeteor protection, and service systems. This standardization will reduce the cost of the transport development and building.
The transport will be delivered to the Moon by the heavy lunar lander.
UNIVERSAL (RESIDENTIAL AND AIRLOCK) MODULE
Universal module
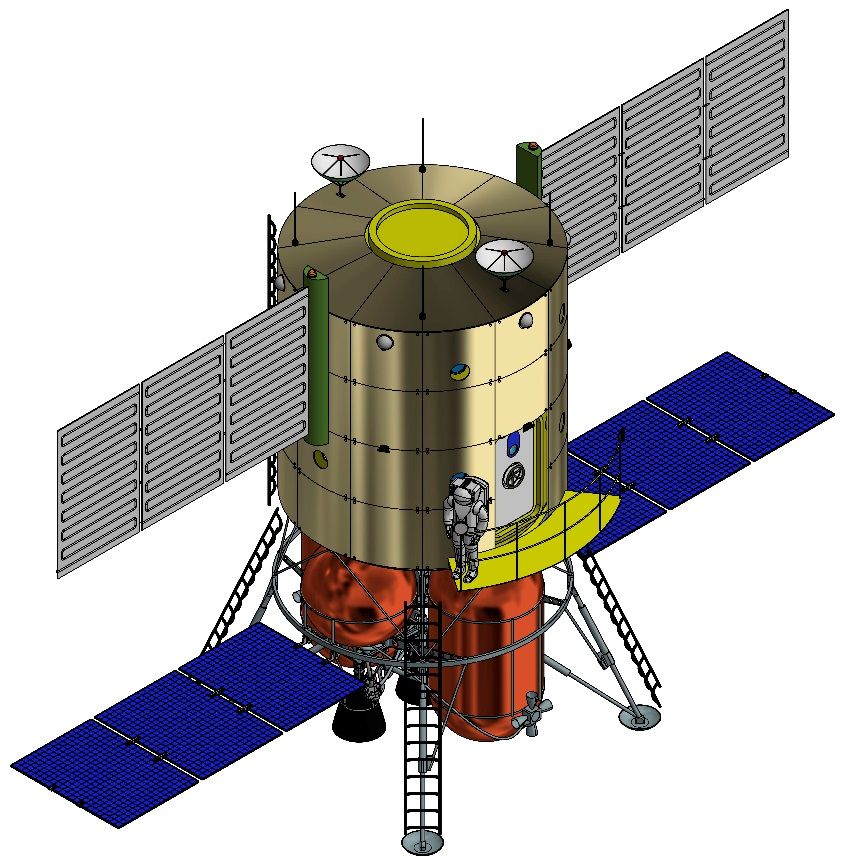
DESCRIPTION
The universal (residential and airlock) module will support the astronauts’ stay on the Moon and their work on the lunar surface, including while building the Base or participating in non-related expeditions.
Arriving on the Moon in a manned spacecraft, switching to the universal module and staying in it for a sufficiently long time (at least a month), the astronauts could make a sufficient number of exits to the lunar surface to conduct scientific research or build the Lunar Base.
The module has two tiers (floors). The ground floor accommodates an airlock, airlock equipment, supplies for exits to the lunar surface, service equipment and systems. The top floor houses the residential compartment, service equipment and systems, supplies for the crew during their stay on the Moon, and other systems.
The module is delivered to the Moon by the heavy lunar lander.
Lunar Roving Vehicles
SELF-PROPELLED MODULAR PLATFORM
Self-propelled modular platform
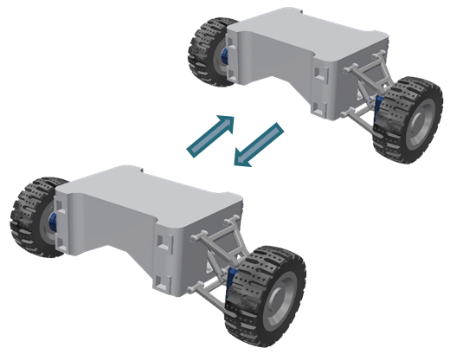
Basic vehicle
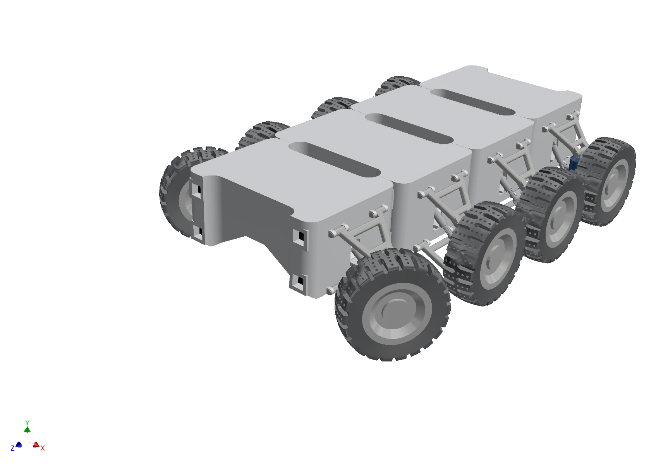
Self-propelled modular platform
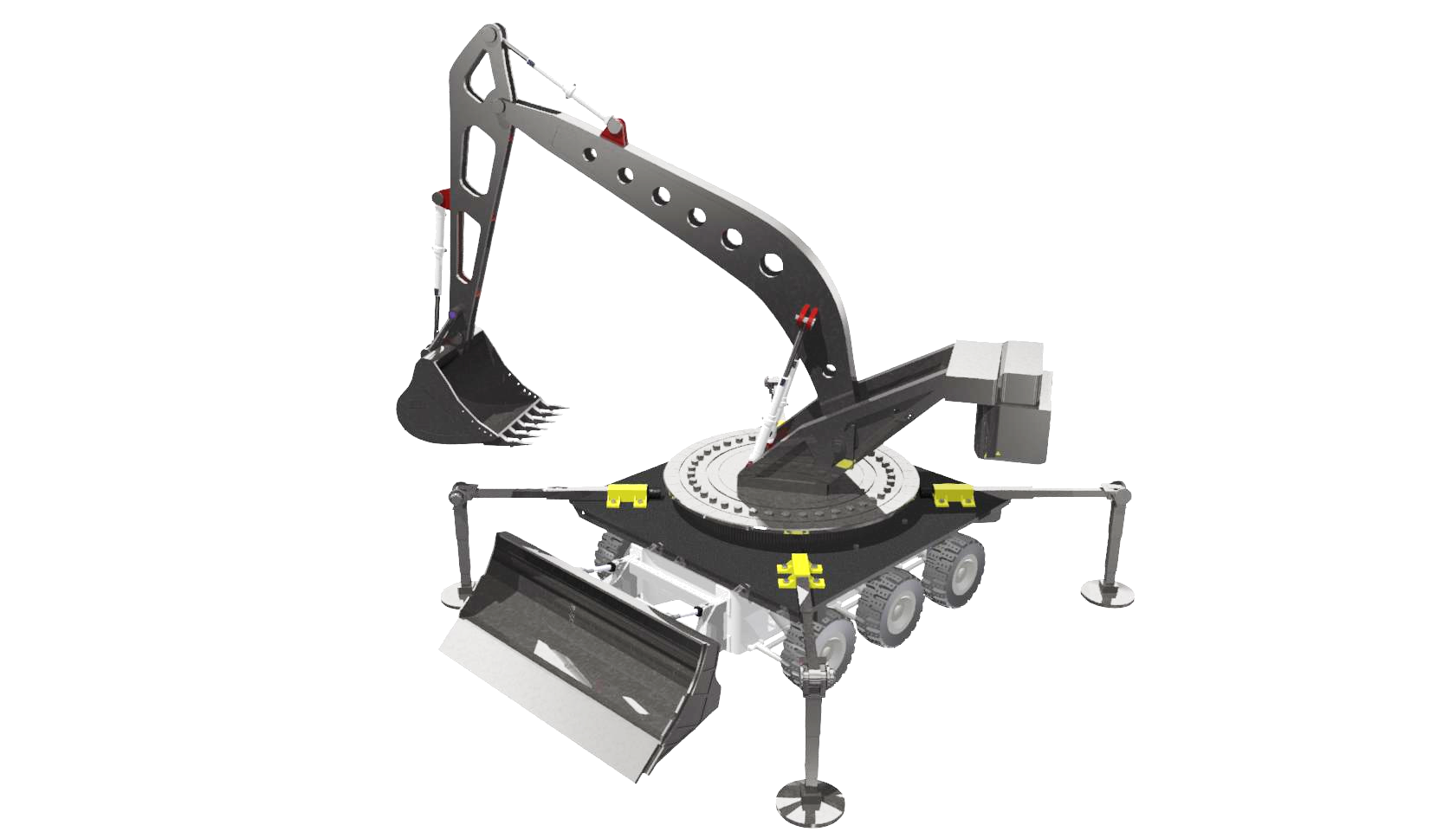
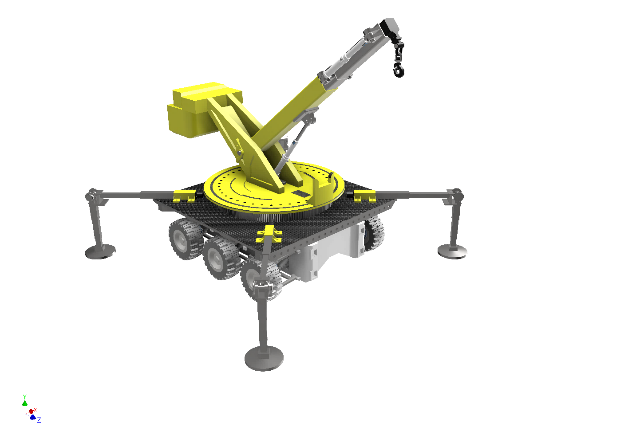
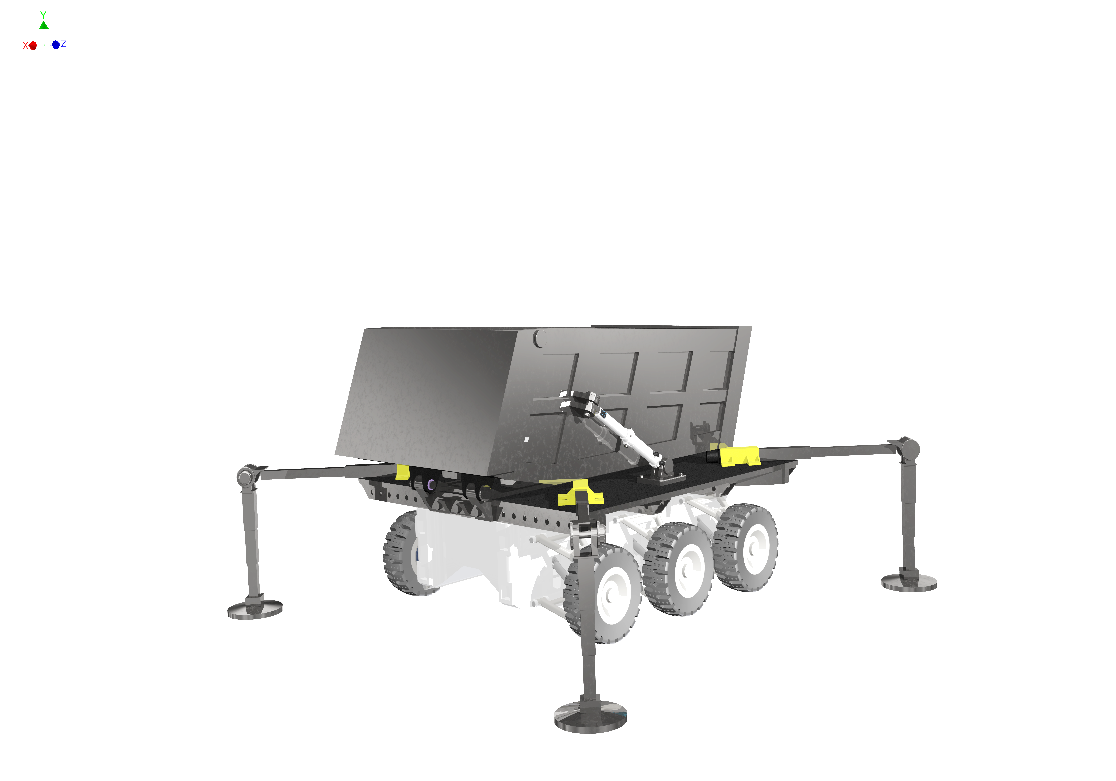
Self-propelled modular platform with different attached implements
DESCRIPTION
The universal (residential and airlock) module will support the astronauts’ stay on the Moon and their work on the lunar surface, including while building the Base or participating in non-related expeditions.
Arriving on the Moon in a manned spacecraft, switching to the universal module and staying in it for a sufficiently long time (at least a month), the astronauts could make a sufficient number of exits to the lunar surface to conduct scientific research or build the Lunar Base.
The module has two tiers (floors). The ground floor accommodates an airlock, airlock equipment, supplies for exits to the lunar surface, service equipment and systems. The top floor houses the residential compartment, service equipment and systems, supplies for the crew during their stay on the Moon, and other systems.
The module is delivered to the Moon by the heavy lunar lander.
SPECIFICATIONS
Type | Overall view of the module | Curb weight, tons | Carrying capacity, tons |
Fixed wheel module | ![]() | m | ~2.6 m |
Castor wheel module | ![]() | m | ~1.4 m |
The dimensions, curb weight, and carrying capacity of one module are defined based on the SMP objective, taking into account the above ratio.
Lines of modules of different standard sizes can be created.
SPECIFICATIONS
ROBOCAR
Robocar for
handling
and soil
excavation
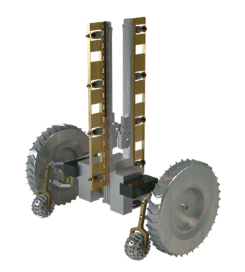
Robocar
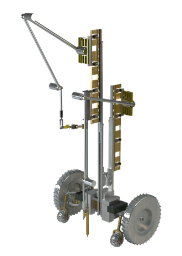
Robocar with a drill

Dump truck
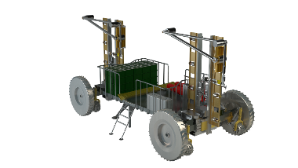
Astronaut’s assistant
Examples of robocar based vehicles
DESCRIPTION
The robocar is a concept of equipment and a method of handling and soil excavation on the lunar surface, which allows performing this work to support research, production, geological exploration and tourism in the context of the Lunar Base.
The basis for handling and soil excavation equipment is a two-wheeled single-axle trolley with vertical lifters, automatic docking devices and manipulators (i.e. a robocar).
Together with selected support equipment (device), a pair of robocars forms an articulated mobile device, easily adaptable to a local terrain profile and capable of moving along an inclined surface and, if required, improving its cross-country capacity.
Handling and soil excavation performed according to the analyzed concept of equipment and method of implementation can significantly reduce the weight of equipment delivered to the Moon, labor intensity, time and cost of the work.
Handling and soil excavation equipment designed to operate in the vicinity of the Lunar Base can support the following basic operations:
• Moving at a specified speed
• Offloading, transportation, tilting and installation of bulky and large-tonnage cargo delivered by the landing platform
• Delivery of the landing platform to the storage or processing site
• Lifting, lowering and moving of small cargos
• Operations with a mechanical manipulator.
LUNAR BASE POWER SUPPLY
SOLAR POWER PLANT
Solar power
plant
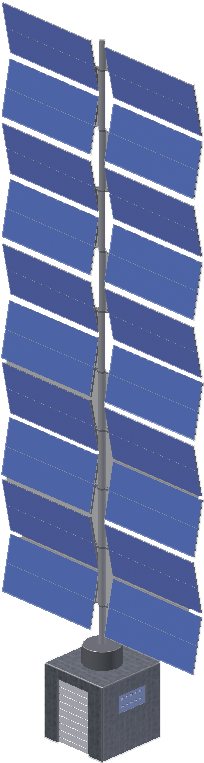
Solar power plant sketch
DESCRIPTION
The solar power plant (SPP) will provide power to the Lunar Base. The SPP is a source of electric power generated by direct conversion of solar energy.
The SPP consists of individual same-type solar panels (modules) operating in parallel. Each module consists of an array of photovoltaic converters based on gallium arsenide (GaAs) heterostructures.
Because electric power can be generated only when the solar panels receive sufficient sunlight, the SPP also includes an energy storage device. When there is enough direct sunlight, the primary power source (solar panels) sends part of the power to a consumer and stores part of the power in the storage device. During the orbital eclipse period, i.e. when there is no direct sunlight, it is the storage device that sends energy to the consumer. Lithium-ion batteries and/or regenerative power plants based on electrochemical generators and an electrolyzer can be such a storage device.
Using the solar power plant has both advantages and disadvantages.
The advantages include:
• Wide application of space-qualified power plants based on solar batteries,
• Generation of electric power without consumption of any materials and zero waste generation,
• Long service life.
The disadvantages include:
• High cost of development, manufacture and delivery to the Moon,
• Relatively high risk of damage due to external factors such as meteorites and moonquakes,
• Degradation of the characteristics of the photoconverters due to exposure to radiation, especially during solar flares.
SPECIFICATIONS
Power plant output power, kW : | |
– typical mode (lunar day) | 10 |
– sleep mode (lunar night) | 1-2 |
– adaptive mode (lunar sunsets and sunrises) | 1-10 |
Solar panels (Sun-oriented): | |
– area, m2; | 100 |
– weight, kg | 480 |
Mass of the electrochemical generator, including propellant mass (60 kg of hydrogen and 540 kg of oxygen), to generate 1 kW/h, kg | 2000 |
Weight of chemical batteries (backup power supply), kg | 820 |
Total SPP mass, kg | 4110 |
Moon Exploration
Lunar Spacecraft
CUBESAT 6U SATELLITE
CubeSat 6U satellite
LUNAR SPACECRAFT
DESCRIPTION
SATELLITE BASIC SPECIFICATIONS
Satellite mass, kg | no more 14 |
Power supply system capacity, W | |
average | 60 – 65 |
peak | up to 130 |
Accuracy of the angular attitude, º | 0.5 |
Accuracy of the angular stabilization, º/s | 0.005 |
Active lifetime, years | 1 |
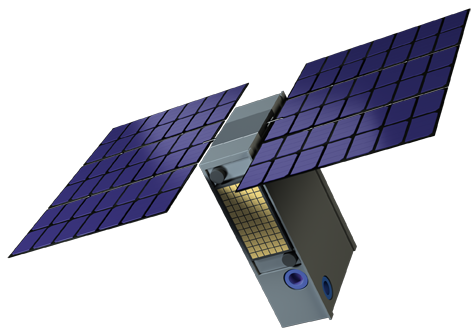
CUBESAT 12U SATELLITE
CubeSat 12U satellite
LUNAR SPACECRAFT
DESCRIPTION
SATELLITE BASIC SPECIFICATIONS
Satellite mass, kg | no more 20 |
Power supply system capacity, W | |
average | 80 – 200 |
peak | up to 230 |
Main propulsion system: | |
working medium | Iodine |
thrust, N | 2× 1.24·10-3 |
total impulse, N•s | 2× 3.7·104 |
Accuracy of angular attitude, º | 0.5 |
Accuracy of angular stabilization, º/s | 0.005 |
Active lifetime, years | 3 |

Lunar landers family
LIGHT-CLASS LUNAR LANDER
Lightweight lunar
lander
LUNAR LANDER FAMILY
DESCRIPTION
The lightweight lander will deliver research equipment or a lightweight lunar rover to the surface of the Moon and carry out the lunar surface research at a landing site.
The lander can deliver a 50-kg payload to the lunar surface and transmit information received by the research equipment on Earth.
The lunar lander is based on the RD840 main engine.
The lander will be operational on the lunar surface for no less than 14 days.
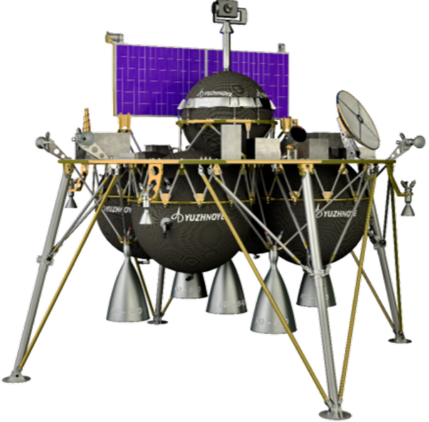
FLYING LUNAR LANDER
Flying lunar lander
LUNAR LANDER FAMILY
DESCRIPTION
The flying lunar lander designed by Yuzhnoye State Design Office will be used for commercial operation and research of the lunar surface at several sites in a single expedition.
The lander can deliver a 50-kg payload (scientific instrumentation) to the lunar surface, carry out research at the landing site, then take off and fly to a new site on the lunar surface.
In total, the lander can support research at up to three sites on the lunar surface, spaced about 20 km apart. The lander can visit two different sites (with a total of three soft landings).
The lander can deliver scientific instrumentation weighing up to 150 kg to the lunar surface without further flights to new areas.
The lunar lander is based on the RD840 main engine.
The lander will be operational on the lunar surface for 14 days from the landing.
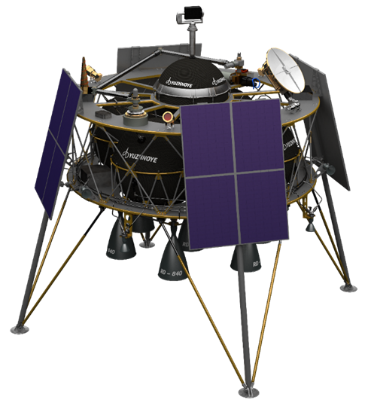
MEDIUM-CLASS LUNAR LANDER
Medium-weight
lunar lander
LUNAR LANDER FAMILY
DESCRIPTION
A medium-weight lunar lander will deliver to the lunar surface the experimental equipment, mobile laboratories, cargo for the Lunar Base, etc.
The medium-weight lunar lender can be expendable or reusable.
The expendable version can deliver payloads from geotransfer or translunar orbit to the lunar surface.
The reusable version can deliver payloads from a circumlunar orbital station to the Lunar Base on the surface and return the lander to the orbital station.
The lander includes the RD860M main engine developed by Yuzhnoye State Design Office.
The lander will be operational on the lunar surface for no less than 14 days.
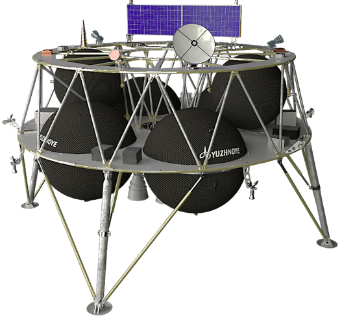
HEAVY-CLASS LUNAR LANDER
Heavy lunar lander
LUNAR LANDER FAMILY
DESCRIPTION
The heavy lunar lander will deliver the delivery transport and the universal module to the lunar surface.
The universal design of the heavy lunar lander will accommodate delivery of both the Lunar Base modules and other payloads weighing up to 10 tons and manned vehicles.
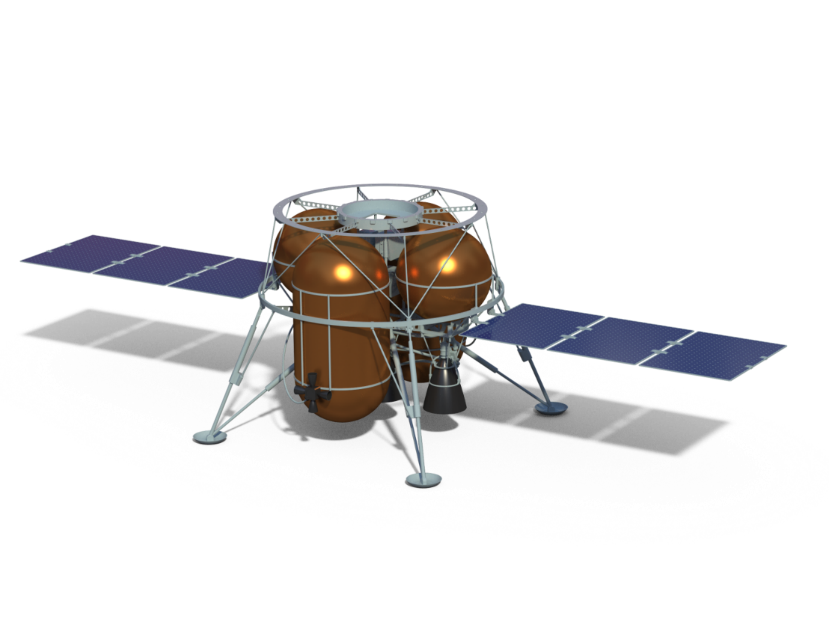
Line of research rovers
LINE OF RESEARCH ROVERS
Line of research rovers
DESCRIPTION
Features of the line of research rovers:
The reconnaissance rover is designed to take photos and videos of the surface and support laser spectrometry studies.
The rover curb weight is 50 kg.
The recon rover is delivered to the lunar surface by the flying lunar lander.
After exploring one area, the recon rover can be relocated to another area by the flying lunar lander. The rover’s high speed and relocation capability allows speeding up the scientific research.
The exploration rover is designed to investigate steep mountain slopes, craters and caves using photo and video cameras, as well as laser spectrometers located on isolated carts.
The rover curb weight is 150 kg. The exploration rover is delivered to the lunar surface by the flying lunar lander.
The geologic rover is designed for geological survey, mainly by drilling wells and extracting samples of regolith from different depths.
The rover curb weight is 600 kg.
The survey can be carried out on the terrain with slopes of up to 10º.
The geologic rover is delivered to the lunar surface by the medium-weight lunar lander.
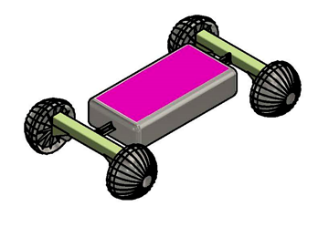
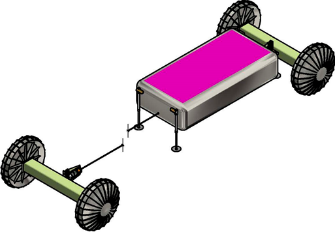
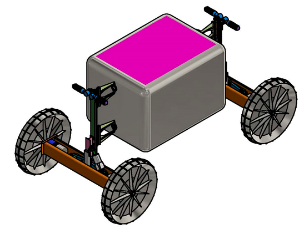
Moon Colonization
Space Transport System
Super-heavy LVs
Launch vehicles Mayak-SH5 and Mayak-SH7
Space Transport System
DESCRIPTION
The Mayak-SH5 and Mayak-SH7 space launch systems are designed for lifting the large-size spacecraft and components of orbital infrastructure, including those of lunar transportation systems, to near-earth orbits.
Burning liquid oxygen and kerosene, the Mayak-SH5 and Mayak-SH7 launch vehicles have serial staging and the design of the Mayak-S3.9 medium-lift launch vehicle enhanced with, respectively, 4 and 6 boosters whose structure is derived from the first stage of Mayak-S3.9. If necessary, these launch vehicles can have a booster for ascending directly to the trajectories towards the Moon and Mars, or a space tug for getting to lunar and near-Mars orbits.
The Mayak-SH5 and Mayak-SH7 launch vehicles operate the RD815 propulsion system in the first stage and the RD872 propulsion system in the second stage, both propulsion systems being developed by Yuzhnoye.
The launch vehicles have a payload fairing 6.2 m in diameter and 25 m long, made of a carbon fiber reinforced polymers. If required, a larger payload fairing can be provided.
SPECIFICATIONS
Launch vehicle | Mayak-SH-5 | Mayak-SH-7 |
Liftoff mass not including the payload, t | 2 246 | 3 101 |
Diameter of stages (fairing), m | 3.9 (6.2) | 3.9 (6.2) |
Propellants | LOX+kerosene | LOX+kerosene |
Launch vehicle height, m | 80 | 80 |
Stage 1 and booster propulsion | 15×RD815 | 21×RD815 |
Stage 2 propulsion | RD872 | RD872 |
Liftoff thrust, tf | 3 769.8 | 5 277.72 |
Maximum payload to orbit, t | ||
– circular orbit (Нcirc=200 km, i=51.6°) | 94 | 133 |
– lunar trajectory | 30* | 40* |
* using a specially designed booster
LUNAR BOOSTER STAGE (LBS)
Lunar booster stage (LBS)
Space Transport System
DESCRIPTION
The boost stage accelerates the transportation system up to the speed required to reach the Moon. The boost stage is based on two RD809K engines.
SPECIFICATIONS
LBS liftoff weight (with payload), tons | 92.6 |
Stage propellants | LOX + kerosene |
Main engine nominal vacuum thrust, tnf | 2×10 |
Engine nominal vacuum specific impulse, s | 352 |
Stage length × diameter, m | 15.5×3.9 |
Payload mass delivered to translunar trajectory, tons | 30.5 |
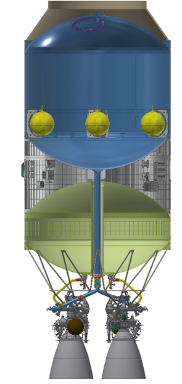
CIRCUMLUNAR BOOSTER TUG
Circumlunar booster tug
Space Transport System
DESCRIPTION
The lunar boost tug (LBT) corrects the trajectory and supports entry into lunar orbit. The tug is based on the RD861K engine.
SPECIFICATIONS
LBT liftoff weight (with payload), tons | 30.5 |
Stage propellants | NTO+UDMH |
Main engine nominal vacuum thrust, tnf | 7.9 |
Engine nominal vacuum specific impulse, s | 330 |
Stage length × diameter, m | 2.5×3.9 |
Payload mass delivered to lunar orbit, tons | 21.3 |
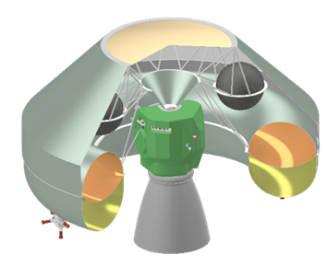
LANDING PLATFORM
Landing platform
Space Transport System
DESCRIPTION
The landing platform will deliver the Lunar Base components (unmanned mission configuration) and the lunar cockpit (manned mission configuration) from a lunar circular orbit to the lunar surface, ensuring their soft landing.
UNMANNED MISSIONS CONFIGURATION
SPECIFICATIONS
Propulsion system, tons | 0.3 |
Control, measurement, power supply, navigation, communication, temperature control, landing systems, tons | 0.4 |
Structure, tons | 0.7 |
Propellant, tons | 8.6 |
Total, tons | 10 |
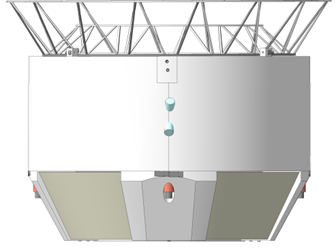
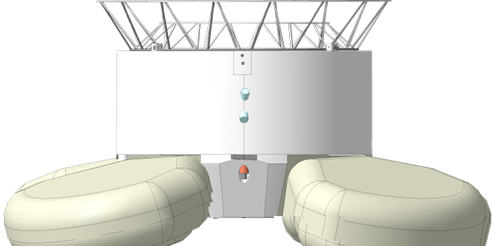
MANNED MISSIONS CONFIGURATION
SPECIFICATIONS
Propulsion system, tons | 0.2 |
Control, measurement, power supply, navigation, communication, temperature control, landing systems, tons | 0.5 |
Structure, tons | 0.2 |
Propellant, tons | 5 |
Total, tons | 5.9 |
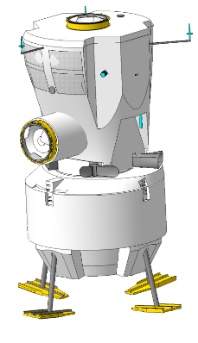
SUPPLY SPACECRAFT
Supply spacecraft
Space Transport System
DESCRIPTION
The delivery transport is designed for periodic delivery to the Lunar Base of consumable supplies, equipment, tools, and spare parts, that is, everything that will be required but cannot be obtained from local resources.
Also, the transport can supply cargo from lunar orbit for landing expeditions in the desired areas (not related to the activities of the Lunar Base personnel).
The transport will be derived from the universal module using its body, antiradiation and antimeteor protection, and service systems. This standardization will reduce the cost of the transport development and building.
The transport will be delivered to the Moon by the heavy lunar lander.
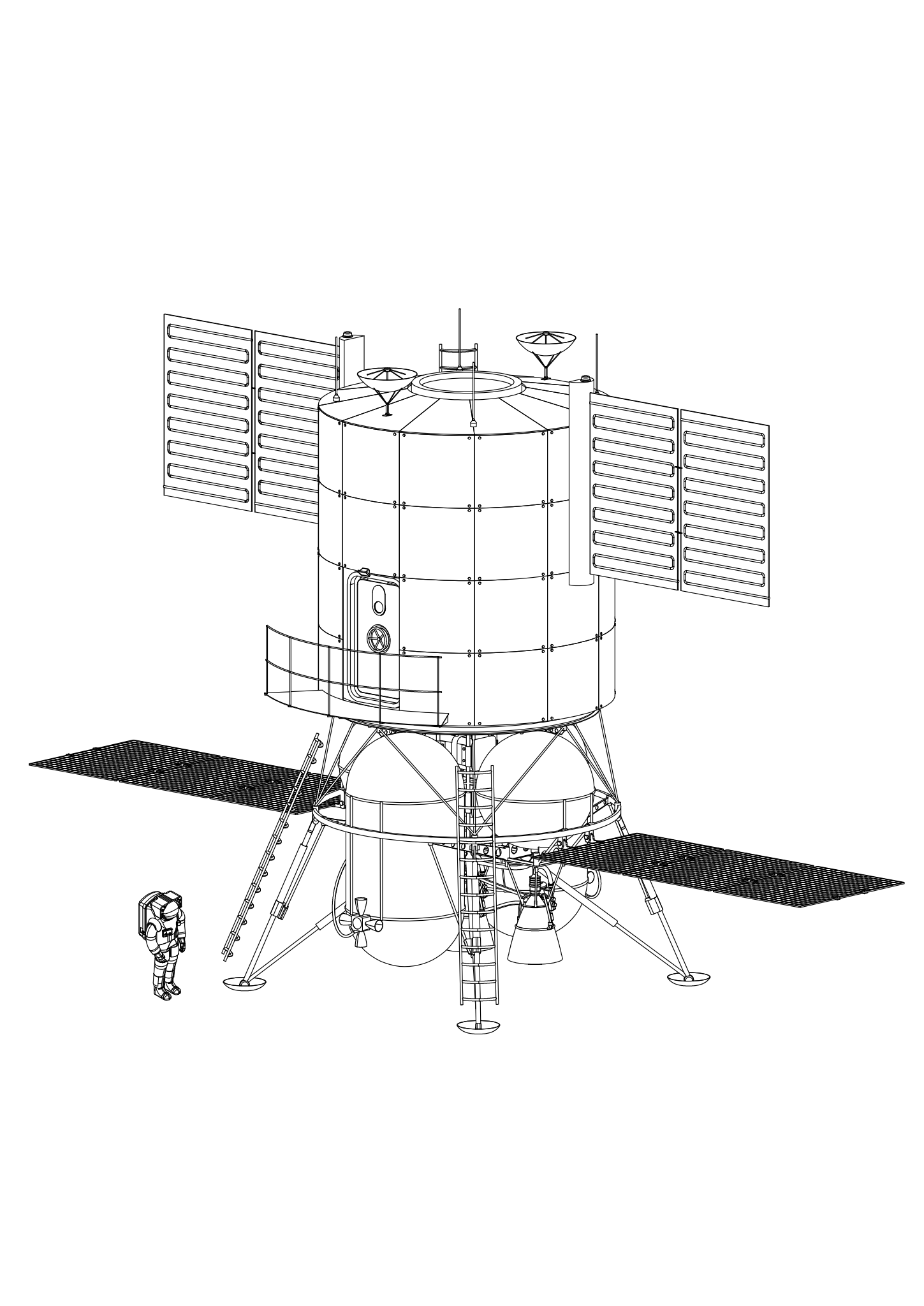
UNIVERSAL (RESIDENTIAL AND AIRLOCK) MODULE
Universal module
Space Transport System
DESCRIPTION
The universal (residential and airlock) module will support the astronauts’ stay on the Moon and their work on the lunar surface, including while building the Base or participating in non-related expeditions.
Arriving on the Moon in a manned spacecraft, switching to the universal module and staying in it for a sufficiently long time (at least a month), the astronauts could make a sufficient number of exits to the lunar surface to conduct scientific research or build the Lunar Base.
The module has two tiers (floors). The ground floor accommodates an airlock, airlock equipment, supplies for exits to the lunar surface, service equipment and systems. The top floor houses the residential compartment, service equipment and systems, supplies for the crew during their stay on the Moon, and other systems.
The module is delivered to the Moon by the heavy lunar lander.
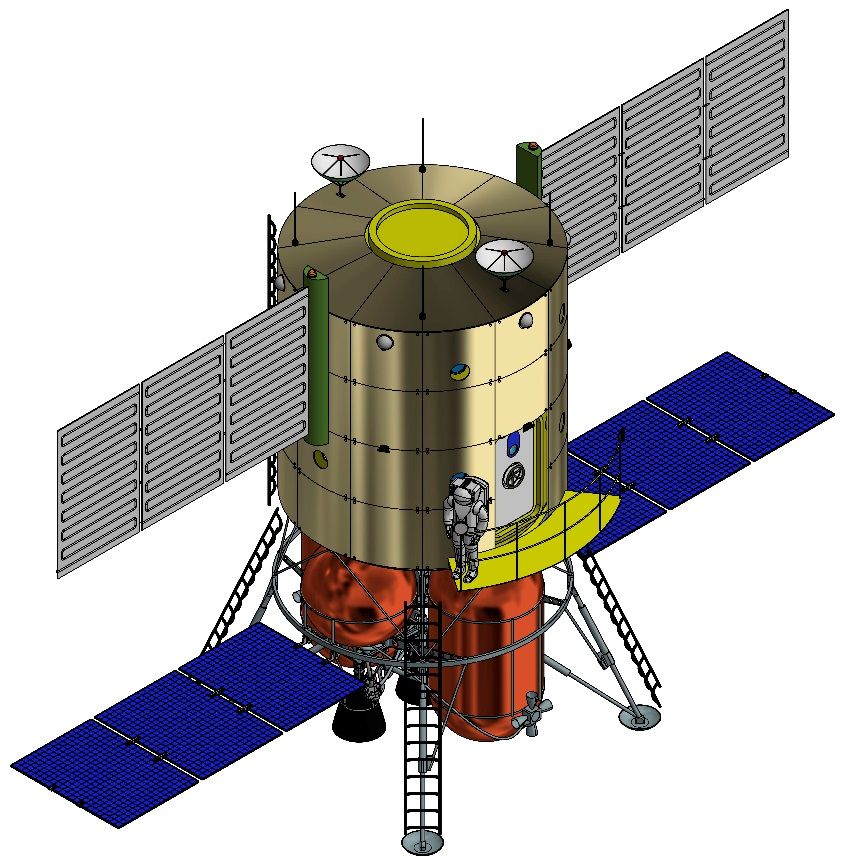
Lunar Roving Vehicles
SELF-PROPELLED MODULAR PLATFORM
Self-propelled modular platform
LUNAR ROVING VEHICLES
DESCRIPTION
The self-propelled modular platform (SMP) is a basic transport vehicle with attached implements to support cargo transportation, as well as construction, assembly, installation and handling work on the surface of various celestial bodies (Moon, Mars, Earth …).
The advantage of building the transportation system based on the self-propelled modular platform equipped with replaceable functional equipment lies in the capability to meet a wider range of challenges with a smaller number of transport vehicles, increasing the intensity and efficiency of using each vehicle. Building the SMP from universal basic modules allows changing the vehicle characteristics within a wide range, ensuring redundancy of the principal functions and systems.
The self-propelled modular platform with an increased carrying capacity is a structure assembled from rigidly interconnected standardized modules, which provides a capability to change the configuration in terms of the number of modules depending on the cargo.
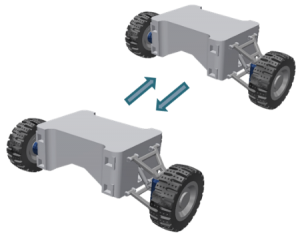
Basic vehicle
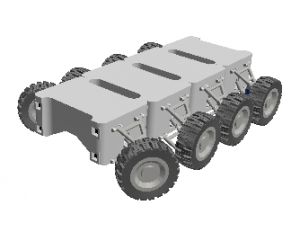
Self-propelled modular platform
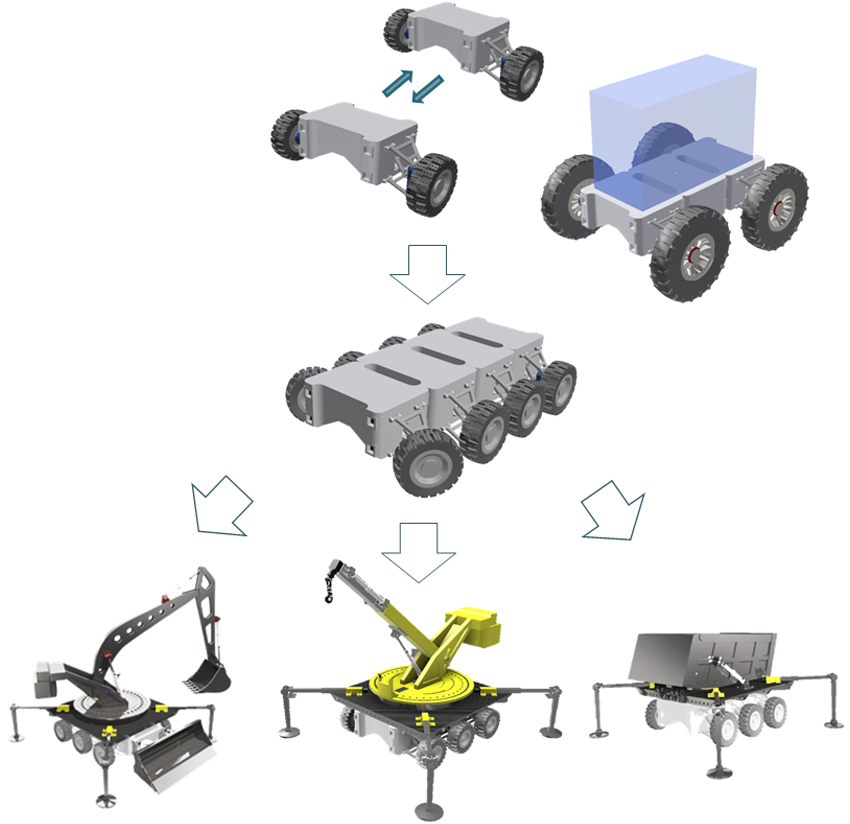
Self-propelled modular platform with different attached implements
SPECIFICATIONS
Type | Overall view of the module | Curb weight, tons | Carrying capacity, tons |
Fixed wheel module | ![]() | m | ~2.6 m |
Castor wheel module | ![]() | m | ~1.4 m |
The dimensions, curb weight, and carrying capacity of one module are defined based on the SMP objective, taking into account the above ratio.
Lines of modules of different standard sizes can be created.
SPECIFICATIONS
Type | Overall view of the module | Curb weight, kg with wheel diameter, m | Carrying capacity, kg | ||||
0.2 | 0.08 | 0.8 | 0.2 | 0.08 | 0.8 | ||
Dedicated SMP for research missions | ![]() | ~50 | ~10 | – | ~100 | ~25 | – |
Universal SMP for cargo transportation, lifting and construction (two modules) | ![]() | ~40 | ~8 | ~2000 | ~80 | ~16 | ~4000 |
Universal SMP (four modules) | ![]() | ~80 | ~16 | ~4000 | ~160 | ~30 | ~8000 |
ROBOCAR
Robocar for handling and soil excavation
LUNAR ROVING VEHICLES
DESCRIPTION
The robocar is a concept of equipment and a method of handling and soil excavation on the lunar surface, which allows performing this work to support research, production, geological exploration and tourism in the context of the Lunar Base.
The basis for handling and soil excavation equipment is a two-wheeled single-axle trolley with vertical lifters, automatic docking devices and manipulators (i.e. a robocar).
Together with selected support equipment (device), a pair of robocars forms an articulated mobile device, easily adaptable to a local terrain profile and capable of moving along an inclined surface and, if required, improving its cross-country capacity.
Handling and soil excavation performed according to the analyzed concept of equipment and method of implementation can significantly reduce the weight of equipment delivered to the Moon, labor intensity, time and cost of the work.
Handling and soil excavation equipment designed to operate in the vicinity of the Lunar Base can support the following basic operations:
• Moving at a specified speed
• Offloading, transportation, tilting and installation of bulky and large-tonnage cargo delivered by the landing platform
• Delivery of the landing platform to the storage or processing site
• Lifting, lowering and moving of small cargos
• Operations with a mechanical manipulator.
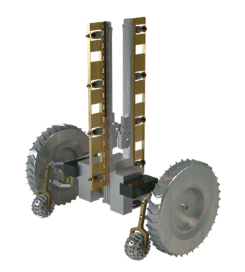
Robocar
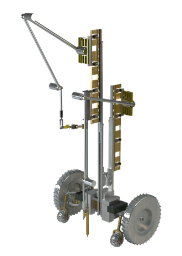
Robocar with a drill

Dump truck
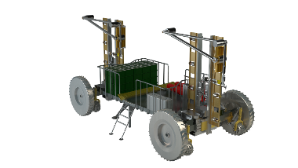
Astronaut’s assistant
Examples of robocar based vehicles
LUNAR BASE POWER SUPPLY
SOLAR POWER PLANT
Solar power plant
LUNAR BASE POWER SUPPLY
DESCRIPTION
The solar power plant (SPP) will provide power to the Lunar Base. The SPP is a source of electric power generated by direct conversion of solar energy.
The SPP consists of individual same-type solar panels (modules) operating in parallel. Each module consists of an array of photovoltaic converters based on gallium arsenide (GaAs) heterostructures.
Because electric power can be generated only when the solar panels receive sufficient sunlight, the SPP also includes an energy storage device. When there is enough direct sunlight, the primary power source (solar panels) sends part of the power to a consumer and stores part of the power in the storage device. During the orbital eclipse period, i.e. when there is no direct sunlight, it is the storage device that sends energy to the consumer. Lithium-ion batteries and/or regenerative power plants based on electrochemical generators and an electrolyzer can be such a storage device.
Using the solar power plant has both advantages and disadvantages.
The advantages include:
• Wide application of space-qualified power plants based on solar batteries,
• Generation of electric power without consumption of any materials and zero waste generation,
• Long service life.
The disadvantages include:
• High cost of development, manufacture and delivery to the Moon,
• Relatively high risk of damage due to external factors such as meteorites and moonquakes,
• Degradation of the characteristics of the photoconverters due to exposure to radiation, especially during solar flares.
SPECIFICATIONS
Power plant output power, kW : | ||
– typical mode (lunar day) | 10 | |
– sleep mode (lunar night) | 1-2 | |
– adaptive mode (lunar sunsets and sunrises) | 1-10 | |
Solar panels (Sun-oriented): | ||
– area, m2 | 100 | |
– weight, kg | 480 | |
Mass of the electrochemical generator, including propellant mass (60 kg of hydrogen and 540 kg of oxygen), to generate 1 kW/h, kg | 2000 | |
Weight of chemical batteries (backup power supply), kg | 8200 | |
Total SPP mass, kg | 4110 |
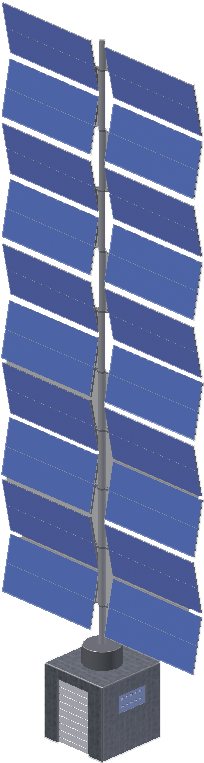
Solar power plant sketch