Services
Services
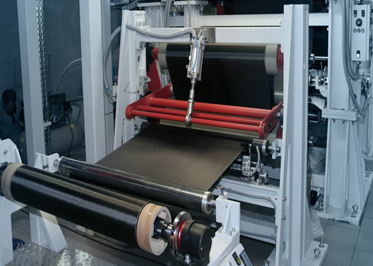
Project description
PRODUCTS FROM POLYMERIC COMPOSITE MATERIALS
The production of assemblies from composite materials is widely used in modern aerospace manufacturing processes. A modern experimental and industrial base has been created at Yuzhnoye SDO, which supports a closed-loop manufacture of products from PCM: from first design concept through to serial production.
The production of assemblies from composite materials is widely used in modern aerospace manufacturing processes. A modern experimental and industrial base has been created at Yuzhnoye SDO, which supports a closed-loop manufacture of products from PCM: from first design concept through to serial production.
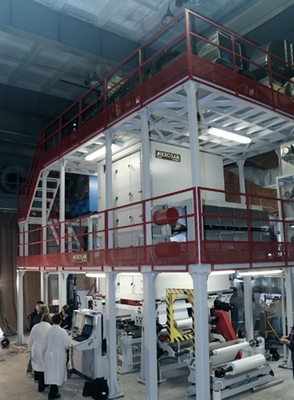
Li 3000-1000 impregnation machine
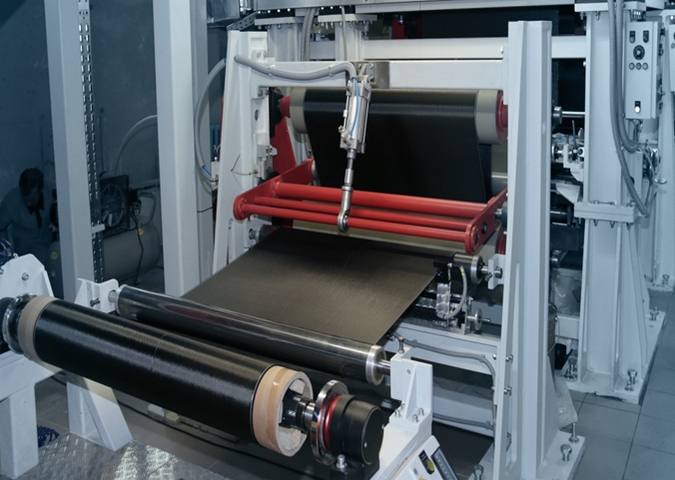
Carbon fiber impregnation process
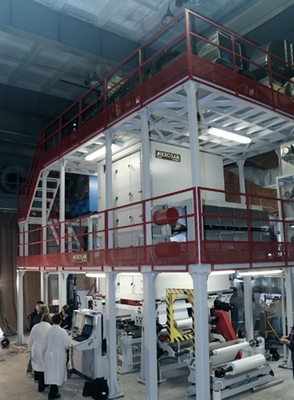
Li 3000-1000 impregnation machine
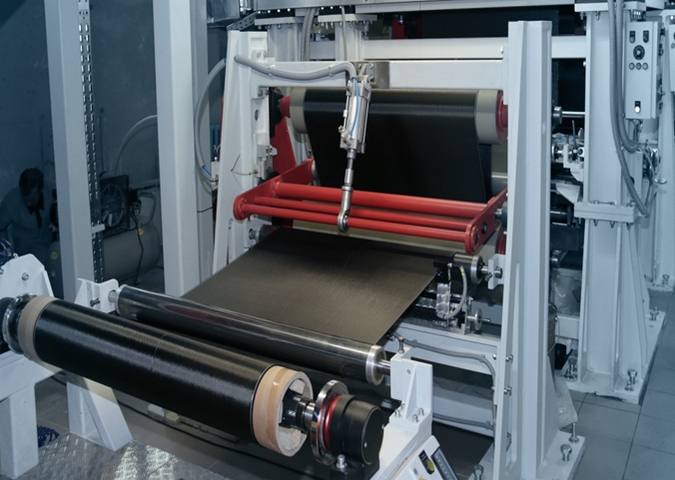
Carbon fiber impregnation process
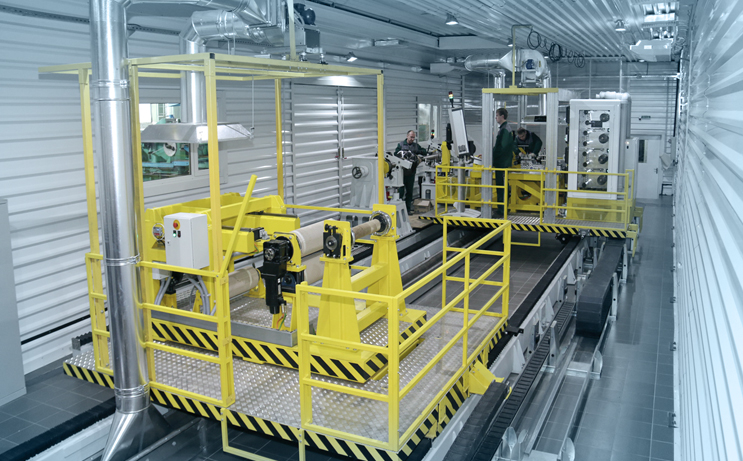
MAW 20 FB5/1 winding machine with CNC
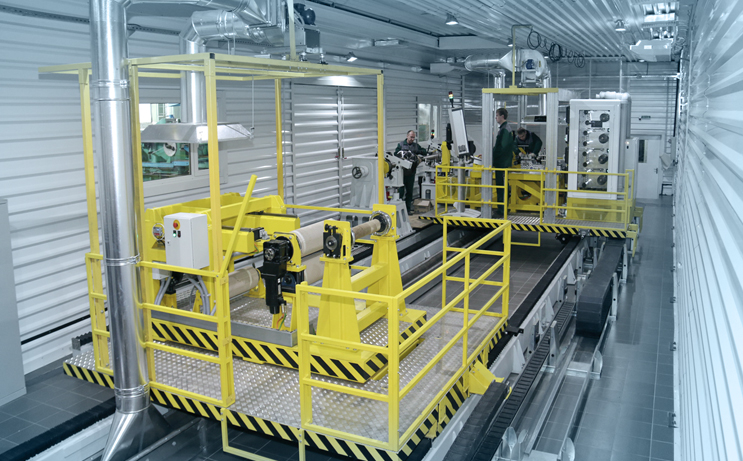
MAW 20 FB5/1 winding machine with CNC
The equipment is designed for the manufacture of the following products:
• Cocoon shells;
• Reinforcing shells for high pressure spherical tanks;
• Dimensionally stable tubular structures;
• Unidirectional prepregs;
• Pipelines.
The epoxy-binder-impregnated carbon fiber wet winding technology is used in the manufacture of solid-propellant motor case load-carrying shells and joints, cones and cone shell reinforcement, high-pressure spherical tank reinforcing shell and tubular elements for spacecraft dimensionally stable frame structures, prototype liner-less cryogenic tanks with small and wide pole holes using carbon fiber flanges, pipelines, etc. Moreover, the dry winding technology allows working with preimpregnated carbon and glass fabrics.
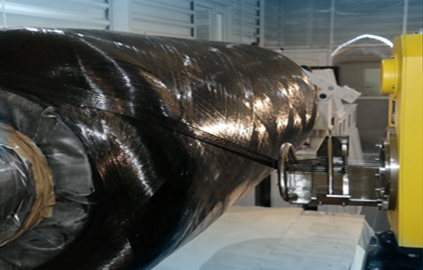
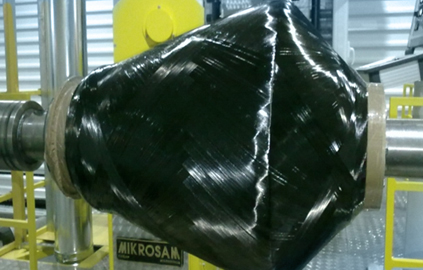
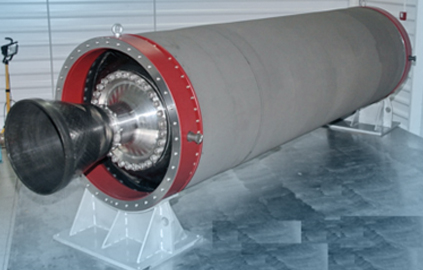
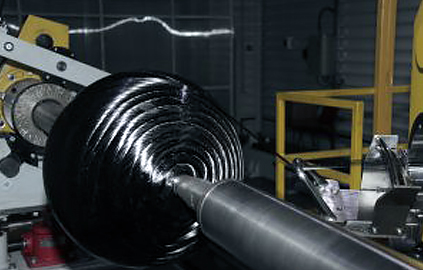
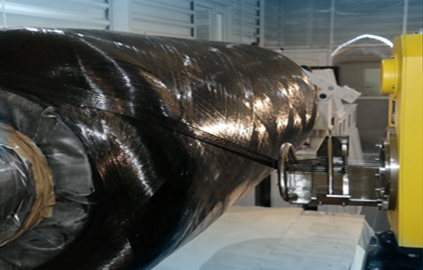
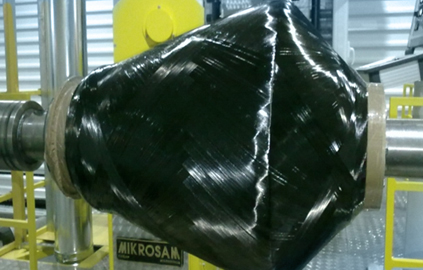
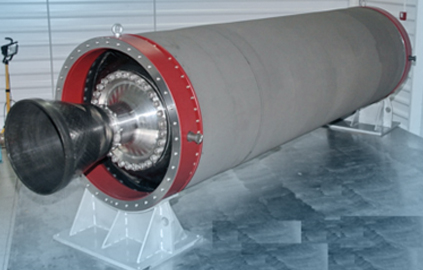
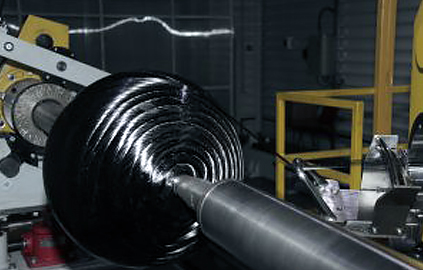
Volume, l | 42 |
Diameter, mm, no more than | 450 |
Working pressure, kgf/cm2 | 346 |
Burst pressure, kgf/cm 2, not less thanе | 692 |
Operating temperature range, °С | – 60 … + 50 |
Mass, kg, not more than | 14 |
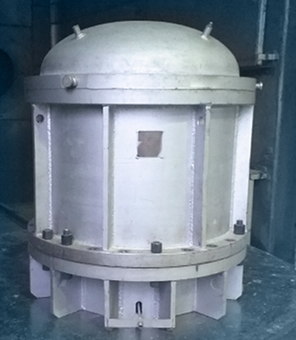
Autoclave
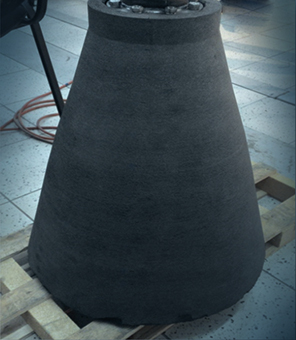
Nozzle skirt
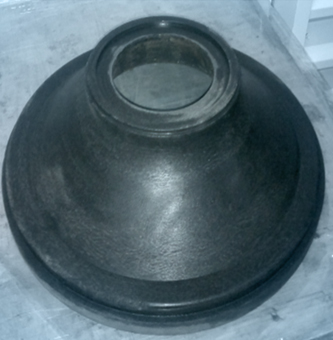
Collar
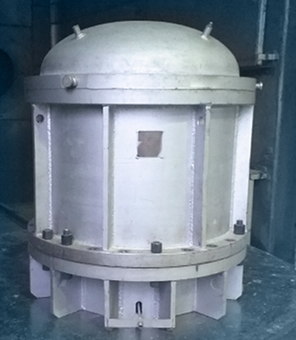
Autoclave
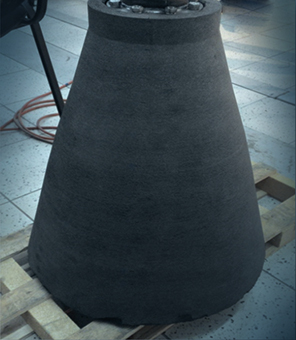
Nozzle skirt
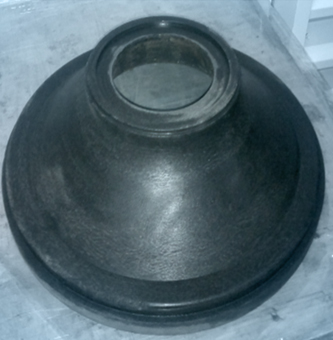
Collar
Applications: SRM nozzle block parts.
The manufacturing techniques are the layering or winding with vacuum autoclave molding, followed by machining and insertion of embedded elements.
Density, kg/m3 | 1300 – 1420 |
Compressive strength , MPa, over | 70 |
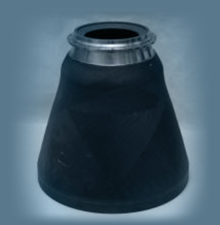
Nozzle skirt with load-bering shell
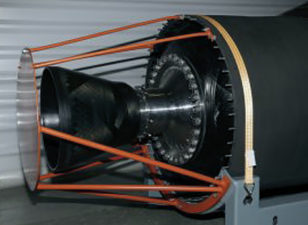
Nozzle skirt attached to MSRM body
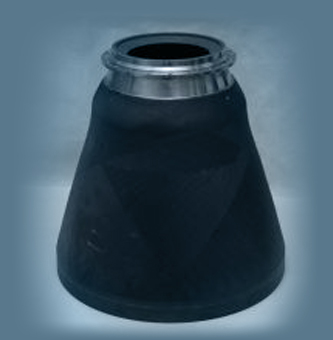
Nozzle skirt with load-bering shell
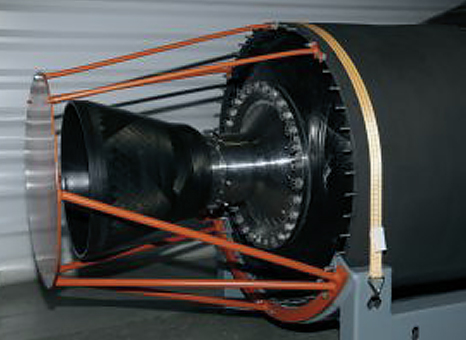
Nozzle skirt attached to MSRM body
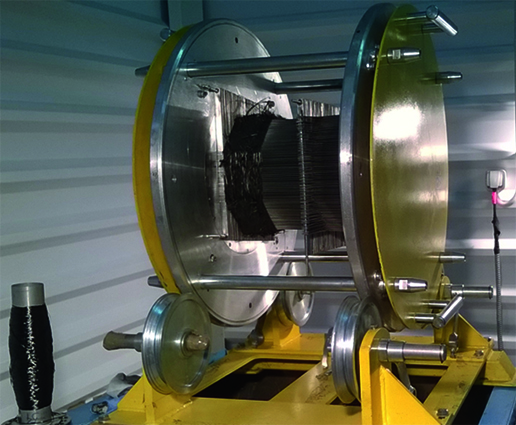
3D reinforced carbon frame
braiding machine
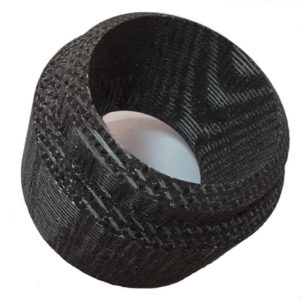
3D carbon-carbon composite material
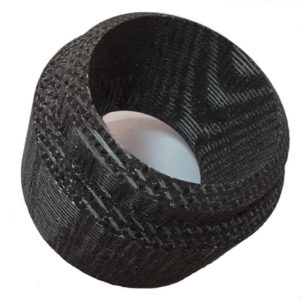
3D carbon-carbon composite material
Diameter , mm | 100 – 500 |
Height , mm | 400 |
Density, kg/m3 | 1700-1800 |
Compressive strength, MPa | ˃ 70 |
Coefficient of linear thermal expansion for temperatures between 20°C and 2000°C | 4 ×10-6 |
Operating temperature (oxygen-free environment), °C | 3000 |
SOLAR PANELS
Three-layer honeycomb structures are used in up-to-date and lightweight products with high stiffness, strength, thermal insulation properties.
Solar panels are used in the photoelectric section of a solar array. Three-layer panels made of carbon fiber shells and an aluminum-foil honeycomb filler are manufactured by press-chamber molding of the shells, followed by the glued assembling of the panel.
Diameter , mm | 100 – 500 |
Height , mm | 400 |
Density, kg/m3 | 1700-1800 |
Compressive strength, MPa | ˃ 70 |
Coefficient of linear thermal expansion for temperatures between 20°C and 2000°C | 4 ×10-6 |
Operating temperature (oxygen-free environment), °C | 3000 |
SOLAR PANELS
Three-layer honeycomb structures are used in up-to-date and lightweight products with high stiffness, strength, thermal insulation properties.
Solar panels are used in the photoelectric section of a solar array. Three-layer panels made of carbon fiber shells and an aluminum-foil honeycomb filler are manufactured by press-chamber molding of the shells, followed by the glued assembling of the panel.
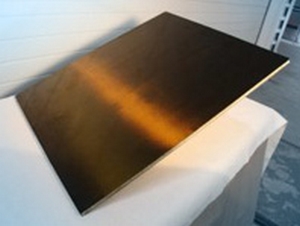
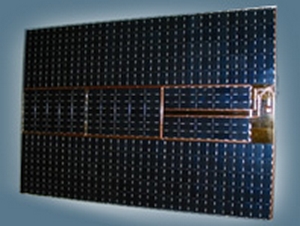
Solar array panel with photoconverters
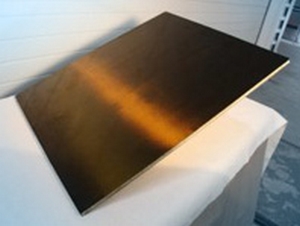
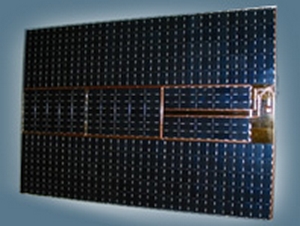
1 m2 mass, kg (12 mm thick panel) | 1-1,3 |
Run-out flatness across the surface, mm, not more than | 1,0 |
Aluminum foil honeycomb filler cell size d=23 μm, mm | 6,0 |
Through-thickness structure thermal conductivity coefficient, W/m•°C | 0,4 |
Skin linear thermal expansion coefficient, 1/deg, not more than | 3,0×10-5 |
SPACECRAFT HEAT SHIELDS
1 m2 mass, kg (12 mm thick panel) | 1-1,3 |
Run-out flatness across the surface, mm, not more than | 1,0 |
Aluminum foil honeycomb filler cell size d=23 μm, mm | 6,0 |
Through-thickness structure thermal conductivity coefficient, W/m•°C | 0,4 |
Skin linear thermal expansion coefficient, 1/deg, not more than | 3,0×10-5 |
SPACECRAFT HEAT SHIELDS
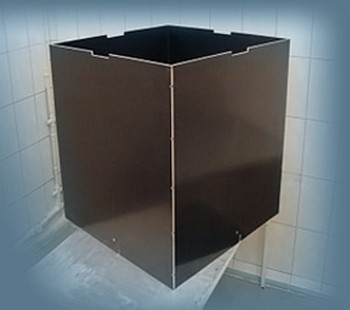
SC heat shields
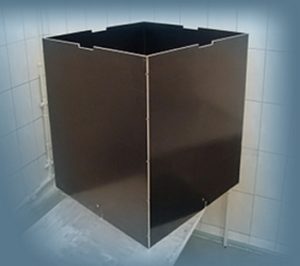
SC heat shields
Heat shields are used for satellite temperature control and protection from outer space environment. Three-layer panels made of carbon fiber shells and an aluminum-foil honeycomb filler are manufactured by press-chamber molding of the shells, followed by the glued assembling of the panel.
1 m2 mass, kg (12 mm thick heat shield) | 1-1,3 |
Run-out flatness across the surface, mm, not more than | 1,0 |
Aluminum foil honeycomb filler cell size d=23 μm, mm | 6,0 |
Through-thickness structure thermal conductivity coefficient, W/m•°C | 0,3 |
SPACECRAFT DIMENSIONALLY STABLE LOAD-BEARING STRUCTURES
Dimensionally stable load-bearing structures are used in spacecraft for the accommodation, positioning, and securing of instruments and equipment during their operations on orbit.
Теплові екрани використовуються для забезпечення теплового режиму космічного апарату та захисту його від факторів космічного простору. Тришарові теплові екрани з використанням вуглепластикових обшивок та алюмінієвого стільникового заповнювача виготовляються за допомогою методу прес-камерного формування обшивок з подальшим клейовим збиранням тришарової панелі.
Маса 1 м2, кг, товщина теплового екрану 12 мм | 1-1,3 |
Неплощинність поверхні, мм, не більше | 1,0 |
Розмір осередка стільникового заповнювача з алюмінієвої фольги δ=23 мкм, мм | 6,0 |
Коефіцієнт теплопровідності конструкції по товщині, Вт/м°С | 0,3 |
РОЗМІРОСТАБІЛЬНІ НЕСУЧІ КОНСТРУКЦІЇ КОСМІЧНИХ АПАРАТІВ
Розміростабільні несучі конструкції космічних апаратів використовуються для розміщення, позиціювання та фіксації апаратури та обладнання під час його експлуатації в космічному просторі.
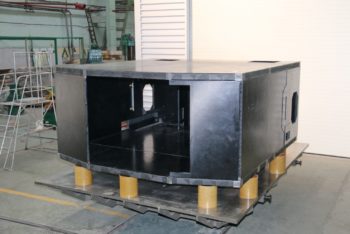
SC dimensionally stable
load-bearing structure
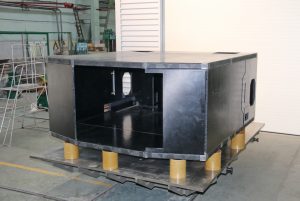
SC dimensionally stable
load-bearing structure
Dimensions (L x W x H), mm | 400×3200×1500 |
Weight, kg | 704 |
Dimensionally stable load-bearing structures combine three-layer panels and carbon fiber reinforced plastic tubes. Three-layer panels with carbon shells and aluminum-foil honeycomb filler are manufactured by press-chamber molding of the shells, followed by the glued assembling of the panel. Carbon tubes are made by the wet winding of carbon fiber.
Dimensions (L x W x H), mm | 400×3200×1500 |
Weight, kg | 704 |
Dimensionally stable load-bearing structures combine three-layer panels and carbon fiber reinforced plastic tubes. Three-layer panels with carbon shells and aluminum-foil honeycomb filler are manufactured by press-chamber molding of the shells, followed by the glued assembling of the panel. Carbon tubes are made by the wet winding of carbon fiber.
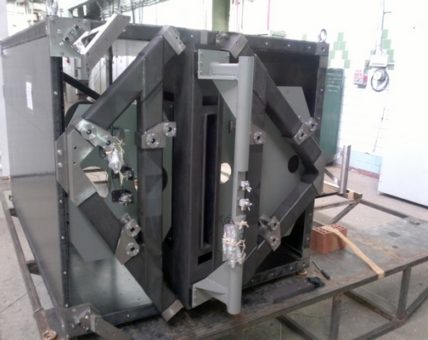
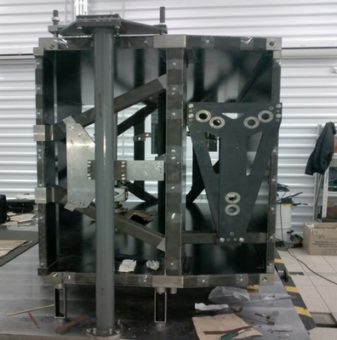
SC dimensionally stable load-bearing structures
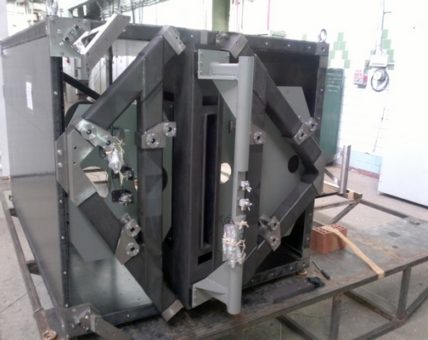
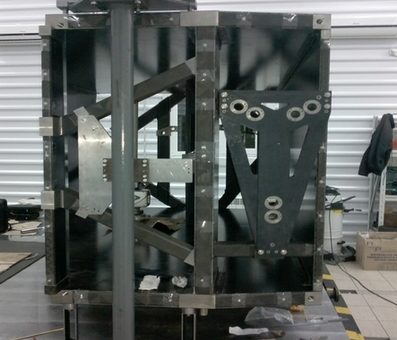
Dimensions (L x W x H), mm | 2380×1532×1272 |
Weight, kg | 190 |
The required dimensional stability of the tubular element is achieved by choosing a reinforcement layout. Depending on the reinforcement layout, dimensional stability can vary from minus 5.0•10-7 to plus 4.3•10-7 1/°С.
tubular element
Length, mm | 600 |
Transverse size, mm | 28х28х2 |
Mass, kg | 0,175 |
Thermal expansion coefficient, 1/°С | – 0,2×10-6 |
Operating temperature range in outer space, °С | – 40 … +50 |
Strain in the operating temperature range, mm, not more than | 0,02 |
The required dimensional stability of the tubular element is achieved by choosing a reinforcement layout. Depending on the reinforcement layout, dimensional stability can vary from minus 5.0•10-7 to plus 4.3•10-7 1/°С.
tubular element
Length, mm | 600 |
Transverse size, mm | 28х28х2 |
Mass, kg | 0,175 |
Thermal expansion coefficient, 1/°С | – 0,2×10-6 |
Operating temperature range in outer space, °С | – 40 … +50 |
Strain in the operating temperature range, mm, not more than | 0,02 |
A wide range of products (from paper to aluminum alloys) are machined on a high-precision CONCEPT 50-60 Z2500 PX5 five-axis machining center with CNC, Italy.
The capabilities of this machining center are multifaceted and unique. The center allows for mechanical processing of products made of Nomex synthetic polyamide, non-metallic composite materials, light alloys, materials with honeycomb and foam structures, ranging from small-sized (matchbox-sized) to large-sized (6000 × 5000 × 2470 mm and a max. mass of 12000 kg) products, including cases and parts of rocket motor nozzles made of carbon fiber and carbon-carbon material.
The equipment combines all operations required for machining (turning, drilling, milling) and offers a number of technological advantages: structural rigidity, reliability, high speed (24000 rpm) and machining accuracy (0.03 mm), protection against abrasive dust, machining process video surveillance and recording, etc.
The machine features a high-performance milling head that can perform along five axes simultaneously (linear – X, Y, Z and rotary A-C). By order of Yuzhnoye SDO, the machine was retrofitted with an additional turning and milling rotary axis. Ultrasonic cutting, which is a technological breakthrough in high-speed machining of modern PCM products, can also be supported.
Spindle power, kW | 32 |
Maximum spindle speed, rpm | 24000 |
Maximum dimensions of the machined product, mm | 6000×5000×2470 |
Maximum workpiece mass, kg | 12000 |
CNC system | SIEMENS 840D Solution Line |
Tool magazine, pcs. | 30 |
Material science research is conducted to measure physical/mechanical and thermal/physical performance of the materials used in
finished products or in technology demonstration samples. During the research, the materials and assemblies are subjected to
incoming inspection, with outgassing of nonmetallic materials measured during exposure to vacuum, leak check procedure verified, and nondestructive inspection of product quality, etc. performed.
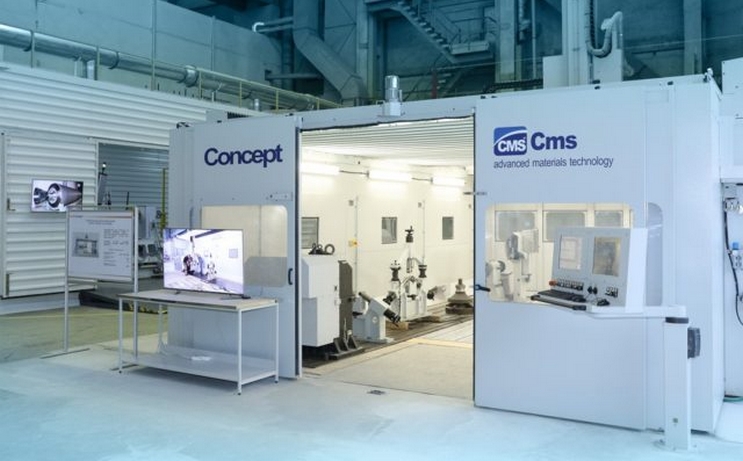
CONCEPT five-axis machining center
A wide range of products (from paper to aluminum alloys) are machined on a high-precision CONCEPT 50-60 Z2500 PX5 five-axis machining center with CNC, Italy.
The capabilities of this machining center are multifaceted and unique. The center allows for mechanical processing of products made of Nomex synthetic polyamide, non-metallic composite materials, light alloys, materials with honeycomb and foam structures, ranging from small-sized (matchbox-sized) to large-sized (6000 × 5000 × 2470 mm and a max. mass of 12000 kg) products, including cases and parts of rocket motor nozzles made of carbon fiber and carbon-carbon material.
The equipment combines all operations required for machining (turning, drilling, milling) and offers a number of technological advantages: structural rigidity, reliability, high speed (24000 rpm) and machining accuracy (0.03 mm), protection against abrasive dust, machining process video surveillance and recording, etc.
The machine features a high-performance milling head that can perform along five axes simultaneously (linear – X, Y, Z and rotary A-C). By order of Yuzhnoye SDO, the machine was retrofitted with an additional turning and milling rotary axis. Ultrasonic cutting, which is a technological breakthrough in high-speed machining of modern PCM products, can also be supported.
Spindle power, kW | 32 |
Maximum spindle speed, rpm | 24000 |
Maximum dimensions of the machined product, mm | 6000×5000×2470 |
Maximum workpiece mass, kg | 12000 |
CNC system | SIEMENS 840D Solution Line |
Tool magazine, pcs. | 30 |
Material science research is conducted to measure physical/mechanical and thermal/physical performance of the materials used in
finished products or in technology demonstration samples. During the research, the materials and assemblies are subjected to
incoming inspection, with outgassing of nonmetallic materials measured during exposure to vacuum, leak check procedure verified, and nondestructive inspection of product quality, etc. performed.