Services
Services
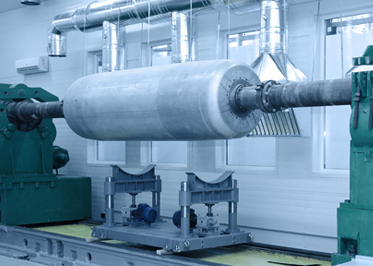
Project description
Thermal protection coatings
The internal heat-resistant coating developed from calendered rubber compounds and designed to protect the motor body from thermal effects during the combustion of solid propellant products. The heat-resistant coating is manufactured by layering with subsequent vulcanization as part of the product.
INTERNAL HEAT-RESISTANT COATING SPECIFICATIONS
Density, not more than, g/cm3 | 1,02-1,08 |
Conductivity factor, not more than (W/kg·K) | 0,244 |
Specific heat, not less than, J/(kg·K) | 1,467 |
A thin-layer heat-resistant coating to protect the launch vehicle exterior surface is developed from aqueous polyurethane dispersions, microspheres, fire retardants, and a number of other additives. Pneumatic spraying is the main method of applying a liquid composition of the exterior heat-resistant coating.
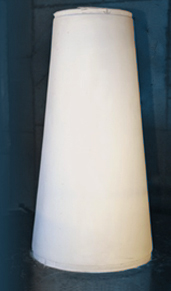
EXTERIOR HEAT-RESISTANT COATING SPECIFICATIONS
Density, g/cm3 | 0,4-0,55 |
Coating working thickness, mm | 0,5-18,0 |
Tensile breaking strength, MPa | 2.0 |
Conductivity coefficient, W/(m·K) | 0,1 |
Specific heat, kJ (kg·K) | 1,6 |
Initial decomposition temperature, °С | 230 |
Maximum decomposition temperature (ablation), °С | 600 |
The ceramic-metal (sintered) heat-resistant coating is designed to protect a liquid-propellant rocket engine turbine flow section. The coating is a composition based on glass, metal and silicon, highly resistant to almost all corrosive environments and characterized by high strength, wear resistance, hardness, low density and stable mechanical properties over a wide temperature range. The coating is applied as a slip mass to the protected surface, which is followed by heat treatment.
CERAMIC-METAL HEAT-RESISTANT COATING OPERATING ENVIRONMENT
Excess oxygen in high-temperature generator gas, % (in terms of mass) | 98-99 |
Gas temperature, °С | 85-600 |
Gas pressure, kgf/cm2 | 100-500 |
Gas velocity, m/s | 50-515 |
Permissible operating temperature, °С | ‒ 155 to + 900 |