International research activities under European initiatives
International research activities under European initiatives
International research activities under European initiatives
HORIZON 2020 PROJECTS
EQUINOX
EQUINOX
A NOVEL PROCESS FOR MANUFACTURING COMPLEX SHAPED FE-AL INTERMETALLIC PARTS RESISTANT TO EXTREME ENVIRONMENTS
Steels and super alloys with considerable amounts of critical raw materials are widely used in many industrial applications, particularly under extreme conditions where corrosion and wear resistance are needed. It is generally accepted, that intermetallics in particular low cost Fe-Al offer outstanding material properties.
Unfortunately, it is difficult to transfer their properties to real products, as intermetallics suffer from low ductility at ambient temperature and poor machinability. The impact of Fe-Al intermetallics as a low cost Cr-free alternative for stainless steel would therefore be much higher if a cost effective industrial process would be available, that allows manufacturing complex 3-D geometries of almost unlimited shapes.
In 2016, Yuzhnoye SDO started works on the research project EQUINOX, which was implemented under Horizon2020 Framework Programme for Research and Innovation of EU.
The main objective of EQUINOX was to develop a novel process that allows to substitute Critical Raw Materials (CRMs) based stainless steel parts used in high volume end consumer products such as in the lock industry, electronics, process industry and automotive industry with a novel near net shape production technology for a new class of highly advanced ductile Fe-Al based intermetallics.
Under the project Yuzhnoye SDO provided expert assessment of applicability of the obtained material in rocket-space products, operating under harsh conditions. The main goal of Yuzhnoye SDO in EQUINOX project was adaptation of EQUINOX material to space rocketry structures.
The main tasks of Yuzhnoye SDO under the project:
The Project was finalized in 2019 with manufacturing and testing of industrial demonstrator of a rocket-space structure. Yuzhnoye SDO manufactured a prototype of the typical turbopump blade, used in liquid rocket engines, and performed a series of its testing in relevant environment, simulating operational loads. The obtained results confirmed outstanding properties of the obtained Fe-Al intermetallic. However, the material of the part was nonhomogeneous which leads to irregular wear. Further research of manufacturing technology is required.
The EQUINOX project was funded by Horizon 2020, the EU Framework Programme for Research and Innovation. Grant Agreement № 685844.
Detailed information is available here: http://equinox-project.eu/
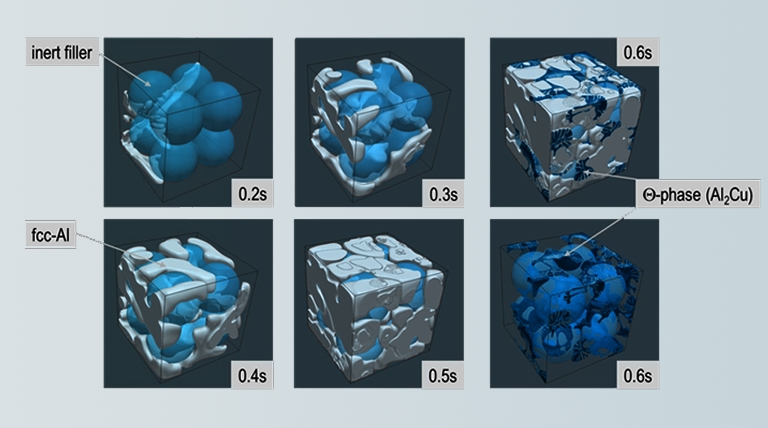
MODCOMP
MODCOMP
MODIFIED COST EFFECTIVE FIBRE BASED STRUCTURES WITH IMPROVED MULTI-FUNCTIONALITY AND PERFORMANCE
Current technological demands are increasingly stretching the properties of traditional materials to expand their applications to more severe or extreme conditions, whilst simultaneously seeking cost-effective production processes and final products.
MODCOMP aims to develop novel fibre-based materials for technical, high value, high performance products for non- clothing applications at affordable cost, with improved safety and functionality.
Within MODCOMP project, Yuzhnoye SDO designed produced and tested structures and prototypes of rocket-space and automotive products from modified materials to validate the impact of modification. Specifically Yuzhnoe SDO performed the following research.
Testing of demonstrators showed improvement (up to18% in resistance to deformation and up to 21% in strength) of the material based on modified CF compared to initial one on samples, cut out of the demonstrators, but not in the structure. Improvement of the CF handling during modification process is required to reach the enhancement in the structure of the propellant tank.
The MODCOMP project was partially funded by Horizon 2020, the EU Framework Programme for Research and Innovation. Grant Agreement №685844.
Detailed information is available here: http://modcomp-project.eu
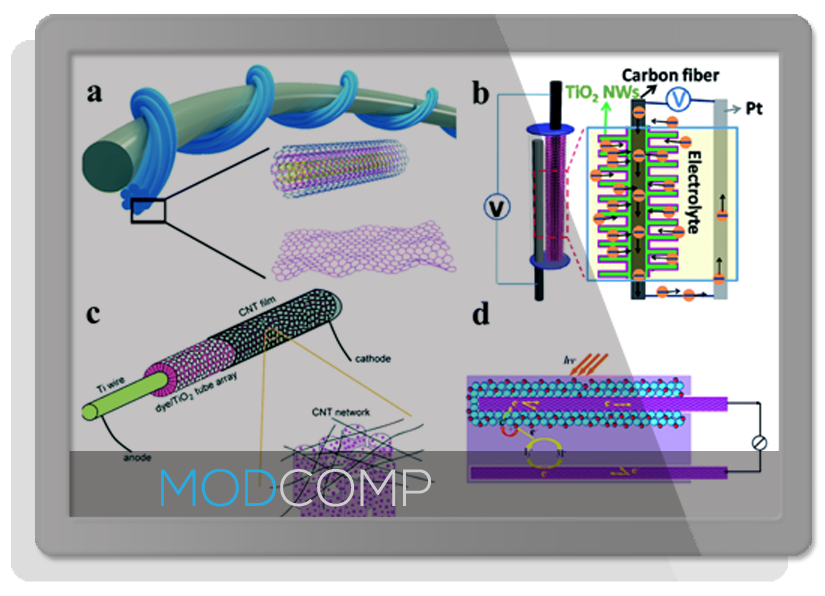
FP7 PROJECTS
FIBRALSPEC
FIBRALSPEC
FUNCTIONALISED INNOVATIVE CARBON FIBRES DEVELOPED FROM NOVEL PRECURSORS WITH COST EFFICIENCY AND TAILORED PROPERTIES
Application of carbon fibers in different branches of industry is expanding with every passed day. This is due to the fact, that strength characteristics of carbon fiber reinforced plastic (CFRP) exceeds analogous characteristics of other structural materials. At Yuzhnoye SDO polymer composite materials based on carbon fibers have been used in the manufacturing of solar panels, load-bearing trusses and thermal shields of spacecraft. Potential capabilities of CFRP application are almost unlimited.
In 2014 Yuzhnoye State Design Office started works on the research project FIBRALSPEC which was implemented under FP-7 Program for Research and Innovation of EU. Main goal of the project was development of prospective carbon fibers from novel precursors with cost efficiency and tailored properties.
Yuzhnoye SDO activities in FIBRALSPEC Project were aimed on integrated detailed testing of carbon fibers, developed under the project, development of technology and equipment for modification of resin as well as validation of developed solutions through manufacturing and testing of demonstrators from modified materials.
As a result of project implementation the technology and equipment for modification of resin with nanoparticles was created and integrated into the existing at Yuzhnoye SDO production line for winding of carbon plastic products. The modification technology was validated by manufacturing and testing of demonstrators of structural elements of the load-bearing truss structure.
This project received funding from the European Union’s Seventh Framework Programme for research, technological development and demonstration under grant agreement №604248.
Detailed information is available here: www.fibralspec.net
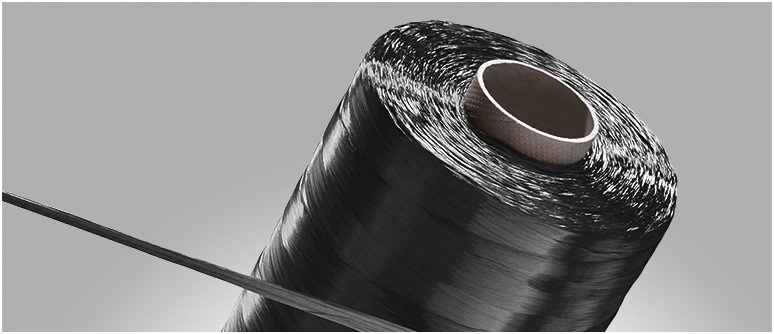
NEWSPEC
NEWSPEC
NEW COST-EFFECTIVE AND SUSTAINABLE POLYETHYLENE BASED CARBON FIBRES FOR VOLUME MARKET APPLICATIONS
Carbon fibers are the most efficient reinforcing materials for composite structures that require high specific strength. Carbon fiber reinforced composites are 80% lighter than steel and 50% lighter than aluminium and provide at least twice stiffness.
However, the extensive use of such material is limited by its high market price. High price of carbon fiber results from the dependence on petroleum-based precursors and the laborious, expensive and non-environmental friendly manufacturing process.
In 2013, Yuzhnoye SDO started activities on FP-7 research project named NEWSPEC. The main objective of the project is development of new carbon fiber through promising low-cost polymers.
In frames of this project Yuzhnoye SDO in cooperation with project partners developed and tested new method of carbon fiber treatment which allow increase its strength characteristics by 15-18% depending on initial quality of a fiber. For project results validation Yuzhnoye developed, manufactured and tested structure mockups of tubes for oil and gas industry and wind blades for wind power plant from treated carbon fibers.
The developed CF treatment technology allows reducing the cost of carbon plastic products due to application of cheaper carbon fiber, strength characteristics of which are significantly improved by treatment.
This project was partially funded under the European Union’s Seventh Framework Programme for research, technological development and demonstration under grant agreement №604168.
Detailed information is available here: www.newspec.eu
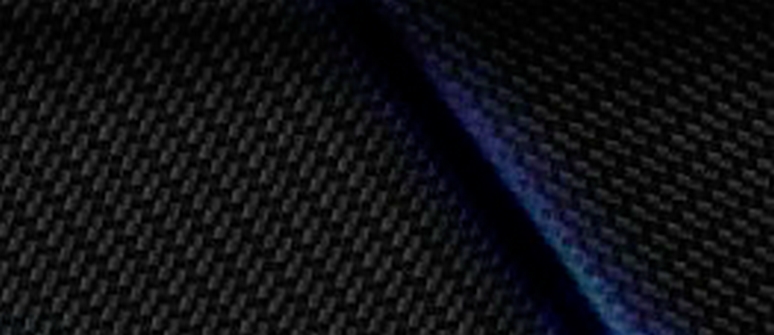
LEOSWEEP
LEOSWEEP
IMPROVING LOW EARTH ORBIT SECURITY WITH ENHANCED ELECTRIC PROPULSION
The space debris problem becomes more and more actual with every space mission. Total weight of space debris at LEO is about 2500 tons (by 2013), and much of it is LVs upper stages. Collisions of spacecraft with space debris objects will become progressively real threat for future space missions.
Getting a capability to deorbit a few types of LVs upper stages is a relevant objective for global space community.
In 2013, Yuzhnoye SDO began works on realization of ambitious research project LEOSWEEP implemented under the FP7 Program of EU. The goal of the Project is to demonstrate the technological feasibility of a first active removal mission of a Ukrainian rocket upper stage, using ion beam technology, which provides an efficient and low-risk contactless manipulation of the debris to be deorbited.
In frames of LEOSWEEP project Yuzhnoye SDO activities were focused on demonstration mission design of LV upper stage removal with ion beam from nearby orbiting shepherd spacecraft and safety analysis of operation and upper stage reentry.
Analysis of the effect of ion beam irradiation on material of the outer surface of the Cyclone-3 LV upper stage was performed. Material sample of outer surface was manufactured and tested in simulated space environment validating safety of contactless manipulation of the object with ion beam. Analysis of the survivability of the LV upper stages during reentry showed that some parts of engine and propellant tanks may reach the ground, which requires specific drop zones.
This project was partially funded under the European Union’s Seventh Framework Programme for research, technological development and demonstration under grant agreement №607457.
Detailed information is available here: www.leosweep.upm.es
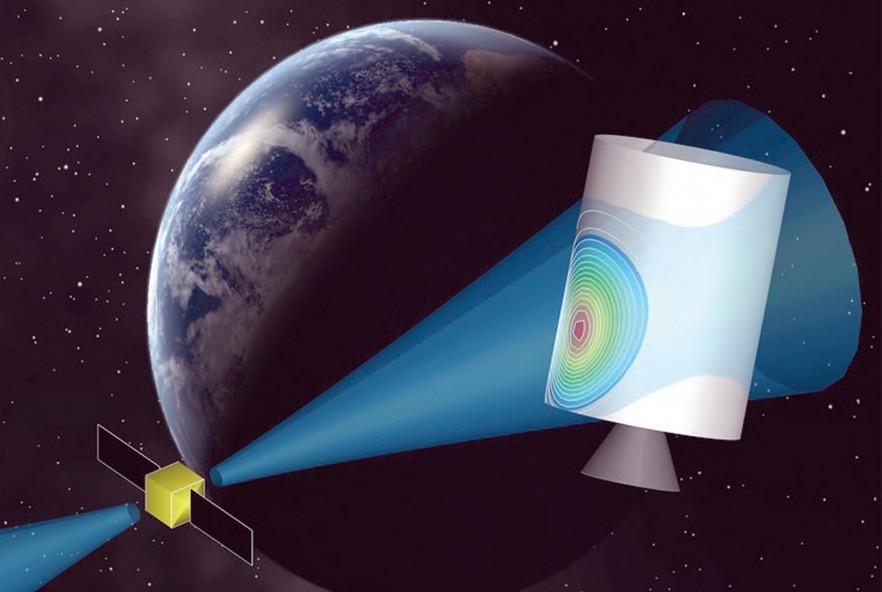
Light-TPS
Light-TPS
SUPER LIGHT-WEIGHT THERMAL PROTECTION SYSTEM FOR SPACE APPLICATION
Interest in light Thermal Protection System (TPS) of reusable spacecraft is increasing worldwide, however, there is no thermal protection system, which has affordable cost, processability and maintenance ability as well as high reliability during operation.
LIGHT-TPS Project was aimed at development of new super-light TPS for various space applications, above all for reusable spacecraft, capable of operating within the entire range of working temperatures.
The main tasks of the project were development of innovative materials (metallic and ceramic), new structure design and manufacturing technologies for the fabrication of new generation thermal protection systems.
In frames of the Project Yuzhnoye SDO was responsible for development of metallic thermal protection system and implementation of the full set of its ground testing to validate its reusability.
It was designed a new structure of TPS which provides fast and cost-effective interflight maintenance and replacement of degraded tiles. New metallic alloys based on chromium and niobium, combined with optimized tile structure, allow meeting the specific mass limit of 10 kg/m2 for metallic part of TPS. Manufactured demonstrators of metallic TPS tiles passed extensive ground testing, simulating reentry conditions on the surface of the spacecraft. Non-destructive inspection methods were optimized for verification of various possible defects and degradation of metallic TPS in operation. As a result of the project Yuzhnoye SDO obtained a patent for the developed metallic TPS structure.
This project received funding from the European Union’s Seventh Framework Programme for research, technological development and demonstration under grant agreement №607182.
Detailed information is available here: http://www.light-tps.eu/
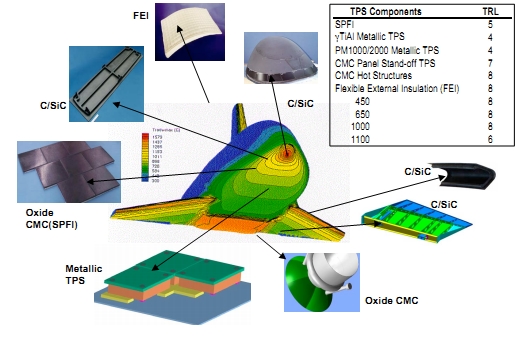
HORIZON 2020 PROJECTS
EQUINOX
EQUINOX
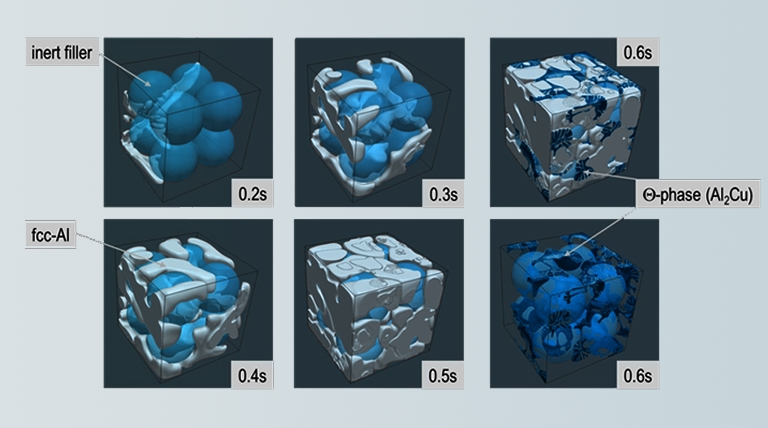
Steels and super alloys with considerable amounts of critical raw materials are widely used in many industrial applications, particularly under extreme conditions where corrosion and wear resistance are needed. It is generally accepted, that intermetallics in particular low cost Fe-Al offer outstanding material properties.
Unfortunately, it is difficult to transfer their properties to real products, as intermetallics suffer from low ductility at ambient temperature and poor machinability. The impact of Fe-Al intermetallics as a low cost Cr-free alternative for stainless steel would therefore be much higher if a cost effective industrial process would be available, that allows manufacturing complex 3-D geometries of almost unlimited shapes.
In 2016, Yuzhnoye SDO started works on the research project EQUINOX, which was implemented under Horizon2020 Framework Programme for Research and Innovation of EU.
The main objective of EQUINOX was to develop a novel process that allows to substitute Critical Raw Materials (CRMs) based stainless steel parts used in high volume end consumer products such as in the lock industry, electronics, process industry and automotive industry with a novel near net shape production technology for a new class of highly advanced ductile Fe-Al based intermetallics.
Under the project Yuzhnoye SDO provided expert assessment of applicability of the obtained material in rocket-space products, operating under harsh conditions. The main goal of Yuzhnoye SDO in EQUINOX project was adaptation of EQUINOX material to space rocketry structures.
The main tasks of Yuzhnoye SDO under the project:
The Project was finalized in 2019 with manufacturing and testing of industrial demonstrator of a rocket-space structure. Yuzhnoye SDO manufactured a prototype of the typical turbopump blade, used in liquid rocket engines, and performed a series of its testing in relevant environment, simulating operational loads. The obtained results confirmed outstanding properties of the obtained Fe-Al intermetallic. However, the material of the part was nonhomogeneous which leads to irregular wear. Further research of manufacturing technology is required.
The EQUINOX project was funded by Horizon 2020, the EU Framework Programme for Research and Innovation. Grant Agreement № 685844.
Detailed information is available here: http://equinox-project.eu/
MODCOMP
MODCOMP
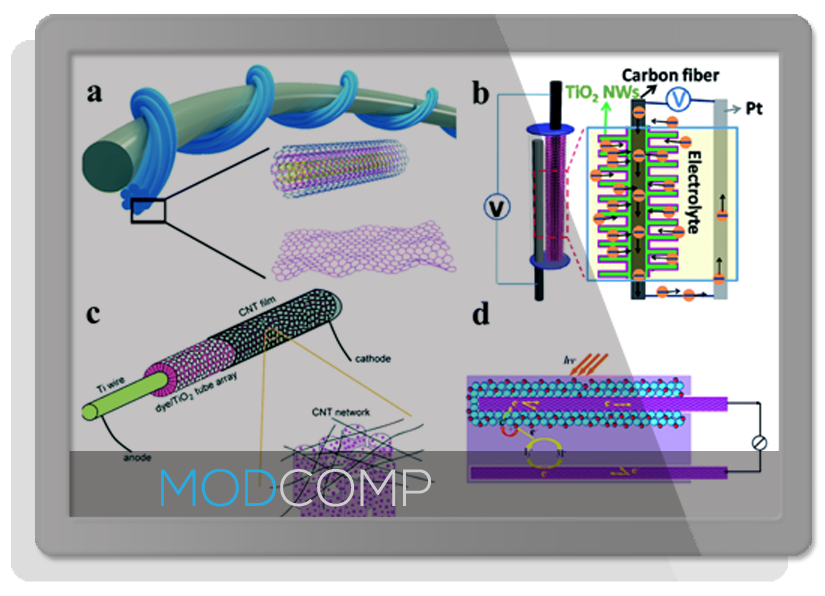
Current technological demands are increasingly stretching the properties of traditional materials to expand their applications to more severe or extreme conditions, whilst simultaneously seeking cost-effective production processes and final products.
MODCOMP aims to develop novel fibre-based materials for technical, high value, high performance products for non- clothing applications at affordable cost, with improved safety and functionality.
Within MODCOMP project, Yuzhnoye SDO designed produced and tested structures and prototypes of rocket-space and automotive products from modified materials to validate the impact of modification. Specifically Yuzhnoe SDO performed the following research.
Testing of demonstrators showed improvement (up to18% in resistance to deformation and up to 21% in strength) of the material based on modified CF compared to initial one on samples, cut out of the demonstrators, but not in the structure. Improvement of the CF handling during modification process is required to reach the enhancement in the structure of the propellant tank.
The MODCOMP project was partially funded by Horizon 2020, the EU Framework Programme for Research and Innovation. Grant Agreement №685844.
Detailed information is available here: http://modcomp-project.eu
FP7 PROJECTS
FIBRALSPEC
FIBRALSPEC
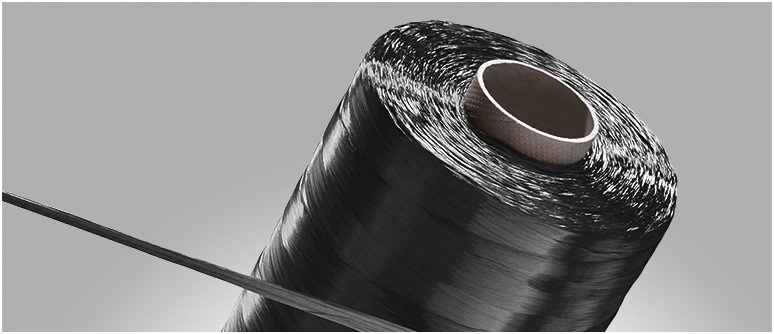
Application of carbon fibers in different branches of industry is expanding with every passed day. This is due to the fact, that strength characteristics of carbon fiber reinforced plastic (CFRP) exceeds analogous characteristics of other structural materials. At Yuzhnoye SDO polymer composite materials based on carbon fibers have been used in the manufacturing of solar panels, load-bearing trusses and thermal shields of spacecraft. Potential capabilities of CFRP application are almost unlimited.In 2014 Yuzhnoye State Design Office started works on the research project FIBRALSPEC which was implemented under FP-7 Program for Research and Innovation of EU. Main goal of the project was development of prospective carbon fibers from novel precursors with cost efficiency and tailored properties.Yuzhnoye SDO activities in FIBRALSPEC Project were aimed on integrated detailed testing of carbon fibers, developed under the project, development of technology and equipment for modification of resin as well as validation of developed solutions through manufacturing and testing of demonstrators from modified materials.As a result of project implementation the technology and equipment for modification of resin with nanoparticles was created and integrated into the existing at Yuzhnoye SDO production line for winding of carbon plastic products. The modification technology was validated by manufacturing and testing of demonstrators of structural elements of the load-bearing truss structure.This project received funding from the European Union’s Seventh Framework Programme for research, technological development and demonstration under grant agreement №604248.Detailed information is available here: www.fibralspec.net
NEWSPEC
NEWSPEC
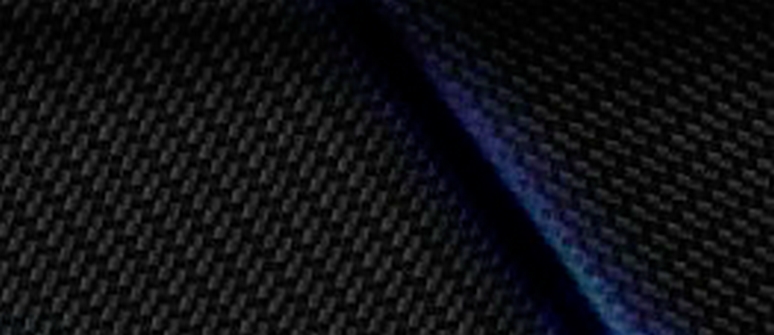
Carbon fibers are the most efficient reinforcing materials for composite structures that require high specific strength. Carbon fiber reinforced composites are 80% lighter than steel and 50% lighter than aluminium and provide at least twice stiffness.
However, the extensive use of such material is limited by its high market price. High price of carbon fiber results from the dependence on petroleum-based precursors and the laborious, expensive and non-environmental friendly manufacturing process.
In 2013, Yuzhnoye SDO started activities on FP-7 research project named NEWSPEC. The main objective of the project is development of new carbon fiber through promising low-cost polymers.
In frames of this project Yuzhnoye SDO in cooperation with project partners developed and tested new method of carbon fiber treatment which allow increase its strength characteristics by 15-18% depending on initial quality of a fiber. For project results validation Yuzhnoye developed, manufactured and tested structure mockups of tubes for oil and gas industry and wind blades for wind power plant from treated carbon fibers.
The developed CF treatment technology allows reducing the cost of carbon plastic products due to application of cheaper carbon fiber, strength characteristics of which are significantly improved by treatment.
This project was partially funded under the European Union’s Seventh Framework Programme for research, technological development and demonstration under grant agreement №604168.
Detailed information is available here: www.newspec.eu
LEOSWEEP
LEOSWEEP
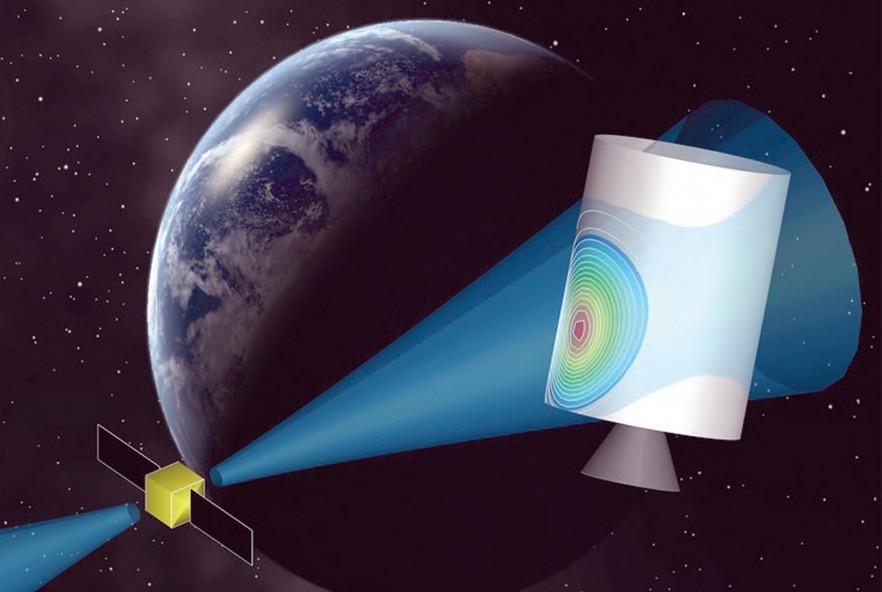
The space debris problem becomes more and more actual with every space mission. Total weight of space debris at LEO is about 2500 tons (by 2013), and much of it is LVs upper stages. Collisions of spacecraft with space debris objects will become progressively real threat for future space missions.
Getting a capability to deorbit a few types of LVs upper stages is a relevant objective for global space community.
In 2013, Yuzhnoye SDO began works on realization of ambitious research project LEOSWEEP implemented under the FP7 Program of EU. The goal of the Project is to demonstrate the technological feasibility of a first active removal mission of a Ukrainian rocket upper stage, using ion beam technology, which provides an efficient and low-risk contactless manipulation of the debris to be deorbited.
In frames of LEOSWEEP project Yuzhnoye SDO activities were focused on demonstration mission design of LV upper stage removal with ion beam from nearby orbiting shepherd spacecraft and safety analysis of operation and upper stage reentry.
Analysis of the effect of ion beam irradiation on material of the outer surface of the Cyclone-3 LV upper stage was performed. Material sample of outer surface was manufactured and tested in simulated space environment validating safety of contactless manipulation of the object with ion beam. Analysis of the survivability of the LV upper stages during reentry showed that some parts of engine and propellant tanks may reach the ground, which requires specific drop zones.
This project was partially funded under the European Union’s Seventh Framework Programme for research, technological development and demonstration under grant agreement №607457.
Detailed information is available here: www.leosweep.upm.es
Light-TPS
Light-TPS
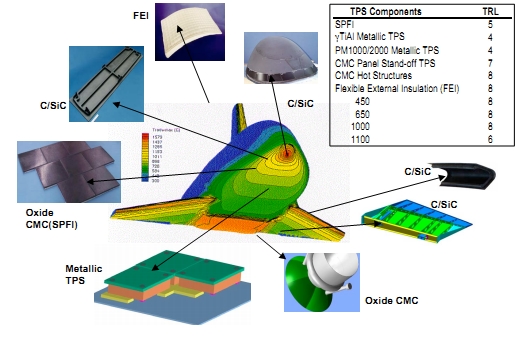
Interest in light Thermal Protection System (TPS) of reusable spacecraft is increasing worldwide, however, there is no thermal protection system, which has affordable cost, processability and maintenance ability as well as high reliability during operation.
LIGHT-TPS Project was aimed at development of new super-light TPS for various space applications, above all for reusable spacecraft, capable of operating within the entire range of working temperatures.
The main tasks of the project were development of innovative materials (metallic and ceramic), new structure design and manufacturing technologies for the fabrication of new generation thermal protection systems.
In frames of the Project Yuzhnoye SDO was responsible for development of metallic thermal protection system and implementation of the full set of its ground testing to validate its reusability.
It was designed a new structure of TPS which provides fast and cost-effective interflight maintenance and replacement of degraded tiles. New metallic alloys based on chromium and niobium, combined with optimized tile structure, allow meeting the specific mass limit of 10 kg/m2 for metallic part of TPS. Manufactured demonstrators of metallic TPS tiles passed extensive ground testing, simulating reentry conditions on the surface of the spacecraft. Non-destructive inspection methods were optimized for verification of various possible defects and degradation of metallic TPS in operation. As a result of the project Yuzhnoye SDO obtained a patent for the developed metallic TPS structure.
This project received funding from the European Union’s Seventh Framework Programme for research, technological development and demonstration under grant agreement №607182.
Detailed information is available here: http://www.light-tps.eu/